4 Gasket Materials for Mid-Range Temperature Sealing
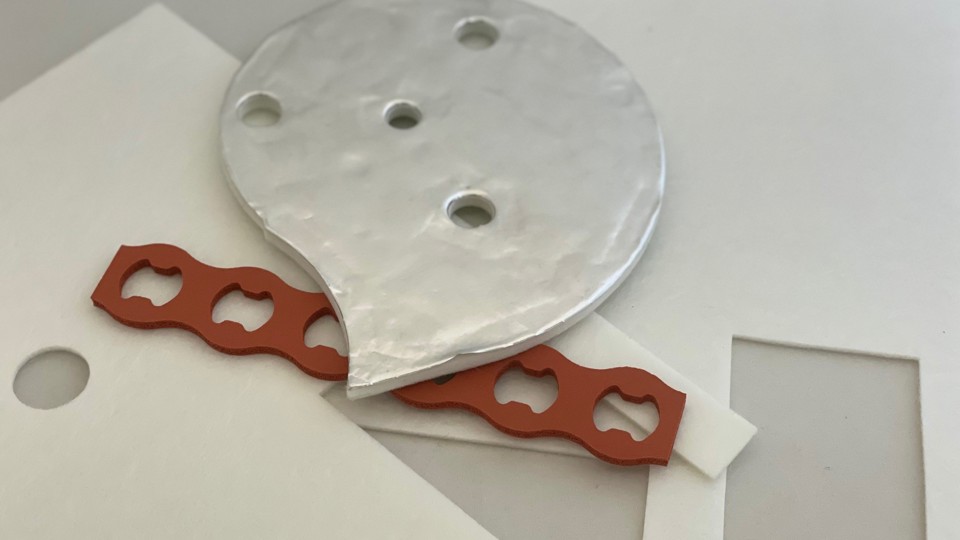
Die-cut gaskets can play a critical role in the overall performance and safety of a part or product. They can endure harsh environments and provide long-lasting, tight seals against air, moisture, chemicals, and other elements. They help insulate against heat and sound and reduce noise, vibration, and harshness (NVH).
But many factors affect the longevity and performance of a gasket. Temperature is one of those variables. High temperatures require different materials than mid- to low-range (or ambient) temperatures.
This blog examines four gasket materials that JBC frequently die cuts that are well-suited for mid-range temperature sealing applications. Let's get started.
1. NOMEX Aramid Fiber
Nomex® fibers are inherently flame-resistant, high-temperature-resistant fibers that will not melt, drip, or support combustion in air. They offer high-temperature durability, superior mechanical strength, and unparalleled chemical stability.
With a thermal rating of 220°C, the material has long been used in electrical insulation applications. Nomex® has a long history as an electrical insulation material of choice for traction motors, automotive motors, and automotive generators due to its proven performance and reliability.
2. Needled Glass Mats
A type of inorganic non-woven fiberglass mat, needle mats have excellent heat insulation and noise mitigation characteristics. Needled glass mat ranges in thickness from .25” up to 1.5”. It is more commonly used as insulation but is easily die-cut on our wide web presses and is suitable for gasketing in some applications.
Needled mats are soft, compressible, binder-free, asbestos-free, and incombustible. There are multiple classifications of needle mats, including ECR Fiber, Basalt Fiber, S Glass, E-glass, HR-glass, and Silica Fiber. Each one offers a unique temperature limit.
Die-cut needle mat gaskets are suitable for appliances, boilers, air conditioners, automotive, and other applications requiring high heat insulation. Needle mat gaskets are suitable for applications that require chemical resistance to acidic, alkaline, and water environments and dielectric properties.
Need an adhesive to aid with assembly or a foil face to reflect radiant heat? Using our extensive laminating capabilities, JBC can laminate your needled glass mats to foils, pressure-sensitive adhesives, and more.
3. Fiberglass
Fiberglass is more cost-effective for die-cut gaskets than ceramic, and it performs well at mid-range temperatures. One of the more popular fiberglass papers is Lydall Manniglas®. ManniGlas® is a non-respirable, glass fiber nonwoven material that is ideal for temperature insulation up to 1000º F (1200°F intermittent). It is available in thicknesses from .015” - .25”.
ManniGlas products also offer strong compression resistance and are commonly used in stoves, boilers and furnaces, hearths, heat trace, and industrial/commercial applications.
ManniGlas papers are available in multiple grades suitable for various thermal, mechanical, handling and cost requirements. It is fabrication-friendly and tough enough for unique die-cut designs. At JBC, per customer request, before die-cutting, we often laminate ManniGlas to light gauge aluminum foil and/or add a peel-and-stick adhesive backing for easier installation.
4. Silicone
When gasket applications require moisture resistance and sealing at temperatures up to 500º F, silicone is a viable material choice. In solid or sponge, silicone demonstrates strong electrical insulating properties and withstands UV, ozone, and oxidation. It is also weather-resistant, flexible, and shrink-proof. It is suitable for applications with a temperature range of -67°F to +500°F.
Die-cut silicone is ideal for various applications, including aerospace parts, engine gaskets, vent ducts, HVAC systems, and industrial and transportation products.
Avoid Overspecification: Work with the Right Converter & Turn to JBC Technologies for Custom Die-Cut Gaskets
Many engineers commonly over-specify materials. For example, just because a combustor or heater runs at 500°F, that doesn’t always automatically mean you need to specify a gasket material rated for continuous use at 500°F. In some cases, the overall design facilitates the natural heat dissipation.
This will produce much lower maximum temperatures at the specific point of the seal. As a result, a lower-cost material could be very well suited to the application without sacrificing product quality, longevity, or performance.
This is why working with an experienced materials converter and die cutter like JBC Technologies is essential. For more than 30 years, JBC has provided expert design and material recommendations to ensure our customers make the best material choice for each unique die-cut application.
Contact us using this easy form or call us at 440-327-4522. Our design and engineering experts team will help ensure you meet or exceed your design specifications without costly over-specification.