5 Reasons to Include Flexible Graphite in your EV Battery Material Stack
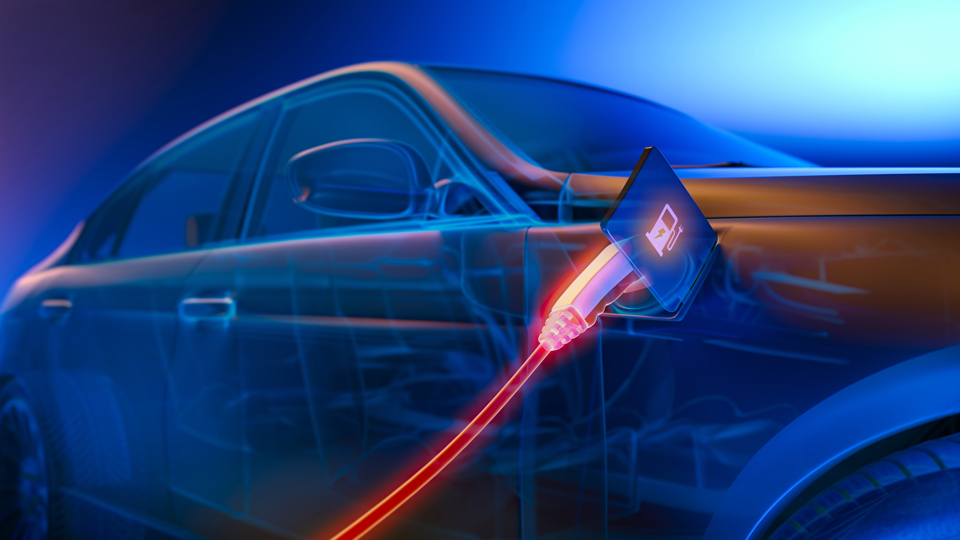
Many of the flexible materials we convert at JBC Technologies have use cases with an electric vehicle battery. Among other things, they are used to mitigate thermal runaway, provide cushioning for battery cells, and in the case of flexible graphite, to keep the battery components at a consistent, uniform temperature while adding an additional layer of thermal runaway protection.
Neograf’s eGraf® SpreaderShield™, for example, is steadily gaining traction as a material of choice within the EV space and has been widely adopted in the marine battery space for nearly a decade. While it can be encapsulated in PET (Mylar), die-cut, and used as a stand-alone product, graphite is more often than not laminated to a material such as Rogers PORON®, Morgan Thermal EST™ Superwool®, or 3M™ FRB and used as an integral layer of a multi-functional material stack.
Today’s post, which features insights and input from Bret Trimmer, Applications Engineering Manager at NeoGraf Solutions, LLC, will highlight five benefits of using a layer of die-cut flexible graphite within an electric vehicle battery—at the pack level, the module level, and in between the battery cells themselves.
Here are five reasons to consider using flexible graphite in your electric vehicle battery:
1—Consistent Battery Temperature
The first and most overarching reason to use flexible graphite between the individual cells, at the module level, or even at the pack level, is its exceptional heat spreading functionality. Graphite is a high-performing, long-lasting material that provides consistent heat spreading. This results in outstanding temperature stability and thermal uniformity of the individual cells during daily operation. It also helps maintain cell temperature uniformity during fast charge and discharge operations and can prevent thermal propagation (thermal runaway) in the event of a cell failure. Graphite can even protect the pack housing from damage in the event of a thermal runaway.
Photo credit: NeoGraf Solutions
2—Faster Battery Charging Time
Drivers of electric vehicles want to be able to achieve a full charge as quickly as possible. But charging too fast can generate excess heat that will damage the cells. Product designers need a way to pull the heat out as fast as it comes in. That is where graphite comes into play. To be clear, you can fast-charge a battery without the graphite layer. Using more concentrated power will result in a faster charge. But without the graphite or other thermal management material to dissipate the heat generated by the quick charging process, the cells will get so hot that you increase the likelihood of damaging them and shortening their useful lifetime. Graphite is not unique in its ability to spread heat. Both copper and aluminum will achieve the same objective, but they come with the added expense of size and weight. For the same heat spreading as aluminum, eGref® SpreaderShield™ is half the thickness and a third of the weight — which leads to our next point.
3—Extended Driving Range
Just as drivers of internal combustion engine (ICE) vehicles want to extend the time between fill-ups, drivers of electric cars want to be able to drive a significant distance without stopping to recharge their car’s battery. This is where the weight of the vehicle becomes increasingly important. The heavier the vehicle, the more energy the motor will need to power the car and the fewer miles you will get per charge.
“Anything you can do to make your battery lighter will help you,” said Trimmer. A lot of the early EVs used aluminum for thermal management. But the thing with aluminum is that it’s thick, and it’s heavy. For the same heat spreading as aluminum, graphite is half the thickness and a third of the weight. This gives an immediate size and weight reduction when you use eGraf® Spreadershield™ in place of aluminum or another metal. If you can make your modules smaller, you can get away with a smaller cold plate, a smaller pack housing, and you’ll need less support structure—all of which further reduce the overall weight of the battery pack. Realistically speaking, moving to graphite for your thermal management layer could equate to a weight savings of 50 to 70 pounds per vehicle.”
4—Longer Battery Life
Batteries work best when they are kept at a constant operating temperature of around 25°C. When a battery gets too hot or too cold, it can become damaged, increasing the likelihood of a fire or other failure mode and reducing the overall life and efficiency of the battery. As indicated above, the purpose of the graphite layer is to maintain a uniform ideal temperature across the cell and remove the excess heat generated during a fast charge or discharge.
“By including proper thermal management materials, you’ll pull heat away from the cells as fast as you generate it. This not only helps to prolong the life of the cells, but it gives you a much safer battery as well,” said Trimmer.
5—Efficient Solution for High-Volume Production
Not only is flexible graphite effective at spreading heat, but it also lends itself well to integration into a streamlined production environment. It is manufactured in large continuous rolls, allowing for efficient die-cutting at a converter, like JBC Technologies, that has extensive experience processing graphite. Collaborating closely, JBC and NeoGraf can help you identify the most efficient part presentation and/or material stack for your application. For example, we can laminate the graphite to one or more other high-performance materials, add a pressure-sensitive adhesive (peel and stick layer) as an assembly aid, or add a pull tab for easy liner removal.
Turn to JBC Technologies for EV Battery Material Converting Needs
For close to two decades, JBC has been putting our engineering and manufacturing expertise to work, transforming flexible graphite rolls into custom die-cut parts that have helped thousands of manufacturers solve critical design challenges. We work directly with NeoGraf Solutions™ to develop efficient die-cutting, packaging, and delivery solutions for their high-quality graphite heat spreading materials that reduce costs and simplify the use and assembly of these parts. Contact us today to put our manufacturing know-how to work for you.
Are you interested in learning more? Give us a call at 440-327-4522 or give us your contact information on this form, and we’ll be in touch soon.