7 Ways to Make Your Die Cut Gasket More Expensive
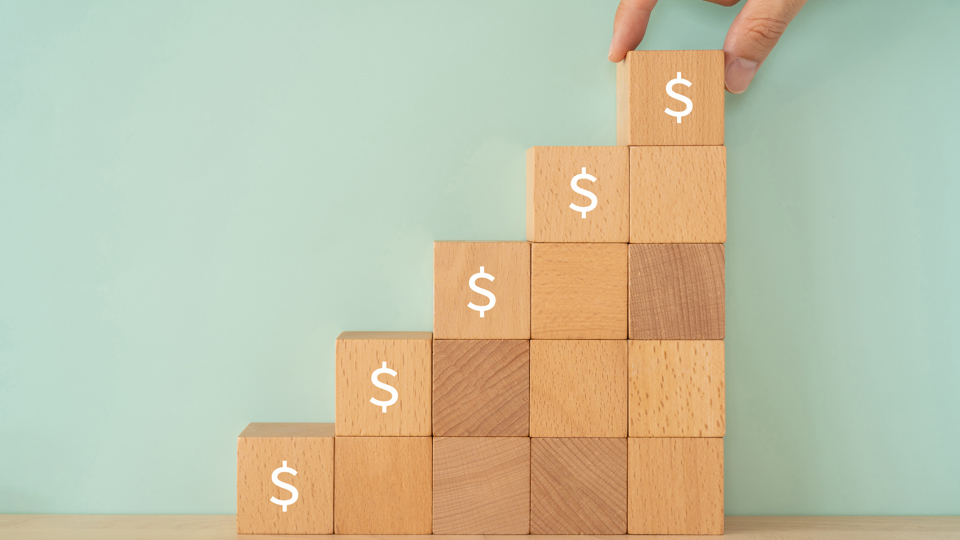
Sourcing an inexpensive die-cut part is simple right? Don’t be too quick to answer that. We’ve seen people make the following mistakes, causing their die-cut parts to cost more:
1. Do everything the same as it’s always been done: Use the same material, don’t consult your supplier, and assume it will work fine.
If you have a part that you’ve been buying for years, chances are materials and processing capabilities have changed. Has your vendor brought new materials and manufacturing processes to your attention? Technologies change fast, and die-cutting is no exception. If it’s been a while since you’ve heard anything new, you may want to think about that.
2. Don’t run your material choice by your vendor.
Failing to ask an expert can result in using an over-engineered product for your application. There are many products that work in many different applications. Not using an expert can cost you. Does your current vendor have material experts on staff? More costly than using an over-engineered material is using one that will fail down the road.
3. Use a die cutter that has limited capabilities because “Small guys have less overhead.”
A supplier with a huge plant, multiple machines, and 100’s of employees HAS to have a lot of over-head right? That may be true, but that doesn’t mean that your parts will be more expensive. What that means is there are redundant processes to ensure your parts get to you on time, material experts that can help you pick the proper material for your application, and engineers that can work with you to design a part that will perform as expected.
4. Use steel rule dies because they are less expensive than rotary.
On the surface, this is absolutely true. Flat-bed dies are cheaper than rotary tools. However, depending on many factors, a more expensive tool can lead to less expensive parts in the long run. Faster processing speeds, higher accuracy, and more flexibility all combine to lower your overall cost.
5. Assume you know what adhesive to use
There are many factors that go into selecting the proper adhesive. Things like substrates, temperatures, life expectancy, and strength all need to be taken into account. With adhesive typically being the highest cost component of the part construction, don’t assume you know what’s best.
6. Don’t tell your vendor how the parts are applied. Assume that pull tabs, easy or tight release liners etc. are a waste of money.
Have you ever seen people using gaskets spending time pulling the liner off the back of your parts? Time is money right? If you’re using a large volume of die-cut parts, a few extra seconds on each of them can lead to hours down the road.
7. Don’t look into having your die-cut supplier assemble parts for you.
If your current supplier can’t assemble your parts with an automated process, you may be spending too much time and money. Robots can apply adhesive parts or add gaskets to your parts extremely efficiently. The person you’re dedicating to this job can add tremendous value in another capacity.
Looking deeper into your current supplier and the parts they provide can end up saving you considerable costs in the long run. Many people don’t like change, but staying the same shouldn’t be comfortable either.