A Guide to ISO Cleanroom Classifications for Medical Device Manufacturing
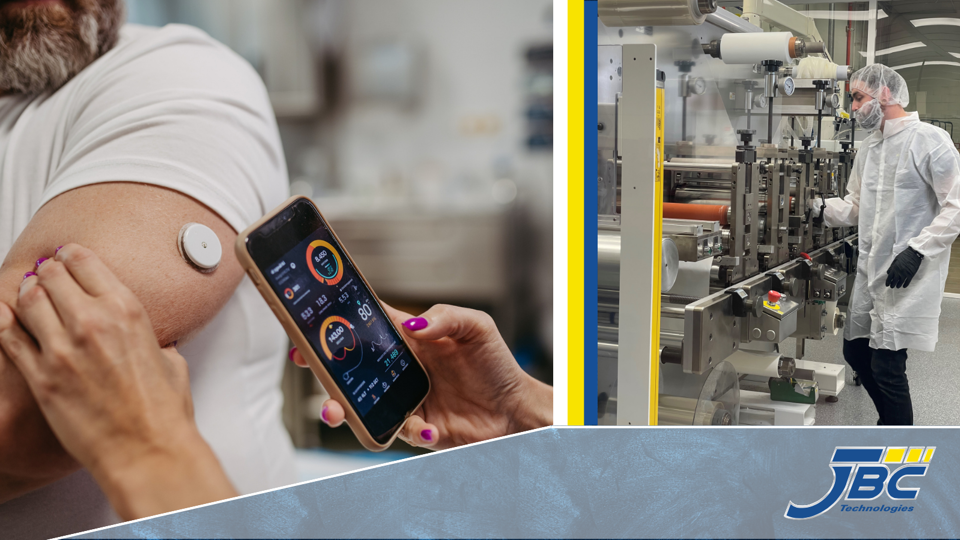
In medical device manufacturing and other highly technical industries, many stringent standards and requirements must be met to ensure optimal part performance and safety. Cleanroom manufacturing offers a controlled environment where contaminants are managed with a great deal of accuracy.
In many applications, cleanroom manufacturing is critical for preventing part failure caused by environmental factors, but not all cleanrooms are created equally. Different products require different cleanliness levels depending on the application of each part, which comes at increasing costs. With the number of cleanroom options available to you, how do you know which one is right for your application? And how do you decide if the manufacturer you are working with has the right environment to suit your production needs?
In this article, we will address:
-
ISO Cleanroom Classifications
-
Examples of parts produced in each cleanroom class
-
How particulate size affects cleanroom selection
Clean Room Classifications
Cleanrooms follow a specific set of categories which range from less clean (ISO 9) to most clean (ISO 1) as defined by the FDA. This post will focus on ISO levels 9-5, which are the most commonly used cleanroom environments. Understanding the differences between these different classifications is essential when deciding which environment your product will need to be produced in. Let's take a deeper look at what these classifications mean.
ISO 9 (Class 1,000,000)
For products such as non-sterile medical device packaging, a general level of cleanliness is required as a baseline but is much less stringent than other ISO levels.
ISO 8 (Class 100,000)
ISO 8 cleanrooms take it up a notch. For the most part, products produced in an ISO 8 cleanroom have external contact with a patient, but do not usually come in contact with sensitive areas of the body. Products like nasal strips, pulse oximetry tapes, and oxygen masks may be done in a Class 8 Cleanroom.
ISO 7 (Class 10,000)
ISO 7 cleanrooms are where we begin to see more products that come into direct contact with patients in more sensitive areas. These more stringent environments are where surgical gowns, wound dressings, and certain diagnostic equipment are made. Parts made in ISO 7 cleanrooms may come into contact with the patient but do not typically go inside the patient's body.
ISO 6 (Class 1,000)
ISO 6 cleanrooms are designed for manufacturing parts that require a high level of cleanliness due to the nature of their bodily application. Parts that will enter the patient’s body, such as catheters, stents, and various surgical instruments are produced here. Although they require a high level of cleanliness for subcutaneous and intravenous applications, they aren’t as susceptible to contamination as implants are.
ISO 5 (Class 100)
Implants like pacemakers and heart valves, as well as sterile injectables, are typically produced in ISO 5 cleanrooms. These products are more susceptible to contamination and require a very high level of cleanliness since they frequently come into direct contact with internal bodily systems.
Particulate Size
Understanding particulate size is an important aspect of navigating cleanroom standards. As outlined in ISO 14644-1, the number of particulates allowed for each cleanroom classification is broken down into different particulate concentrations. Smaller particles are often more difficult to manage and remove from the air, while large particles are easily filtered out. This is why less stringent cleanrooms don’t monitor very small particles, while cleanrooms like ISO 5 and 6 do. Small particles can more easily get into small gaps and critical surfaces on medical devices, so products that are highly sensitive to small particles must be produced in more tightly controlled cleanroom environments.
Proper air filtration is critical to managing particulate concentration in a cleanroom environment. According to the FDA, a HEPA filter must be maintained to ensure aseptic conditions. Air supplied from a HEPA Filter must be supplied in critical areas with enough velocity to remove unwanted particles and maintain unidirectional airflow during operations.
Clean Room Quick Reference Chart
Cleanroom Type |
Stringency Level |
Particles/Cubic Meter |
Applications |
Examples |
ISO 9 |
Low |
≥ 0.1 µm: Not defined ≥ 0.2 µm: Not defined ≥ 0.3 µm: Not defined ≥ 0.5 µm: 35,200,000 ≥ 1.0 µm: 8,320,000 ≥ 5.0 µm: 293,000 |
Non-Sterile clean parts, parts for products produced in higher cleanroom levels |
Orthopedic parts, Medical device packaging, components that will be sterilized later
|
ISO 8 |
Low |
≥0.1 µm: Not defined ≥ 0.2 µm: Not defined ≥ 0.3 µm: Not defined ≥ 0.5 µm: 3,520,000 ≥ 1.0 µm: 832,000 ≥ 5.0 µm: 29,300 |
Parts that have external contact with patient’s body in non-sensitive areas |
Pulse oximetry patches, oxygen masks, nasal strips |
ISO 7 |
Medium |
≥ 0.1 µm: Not defined ≥ 0.2 µm: Not defined ≥ 0.3 µm: Not defined ≥ 0.5 µm: 352,000 ≥ 1.0 µm: 83,200 ≥ 5.0 µm: 2,930 |
Come in direct contact with the patient in more sensitive areas. |
Surgical gowns, wound designs, certain diagnostic equipment |
ISO 6 |
High |
≥ 0.1 µm: 1,000,000 ≥ 0.2 µm: 237,000 ≥ 0.3 µm: 102,000 ≥ 0.5 µm: 35,200 ≥ 1.0 µm: 8,320 ≥ 5.0 µm: 293 |
Necessary for products Placed within patients' body, but not as easily contaminated as implants. |
Catheters, stents, surgical instruments |
ISO 5 |
High |
≥ 0.1 µm: 100,000 ≥ 0.2 µm: 23,700 ≥ 0.3 µm: 10,200 ≥ 0.5 µm: 3,520 ≥ 1.0 µm: 832 ≥ 5.0 µm: 29 |
For products with high level of cleanliness requirements and risk of contamination that go into the body. |
Implants, pacemakers, heart valves |
Adding Value with a Cleanroom Converting Partner
There's no doubt it can be overwhelming when trying to navigate the world of cleanroom standards and regulations.
But that’s where we come in…
Enlisting the help of a specialized converter such as JBC Technologies grants you access to a wealth of engineering expertise and valuable industry relationships. JBC is home to multiple cleanrooms across three of our different facilities with ISO 7-9 cleanroom capabilities. Our capabilities include rotary die cutting, in-line multi-layer lamination, island placement, and automatic defect detection. We don’t just manufacture your part for you, we help you throughout every step of the process from prototyping to high-volume production and can help you determine which cleanroom is necessary for your part.