Die-Cut Flexible Materials: Lighter, Scalable, Aerospace EMI/RFI Solutions
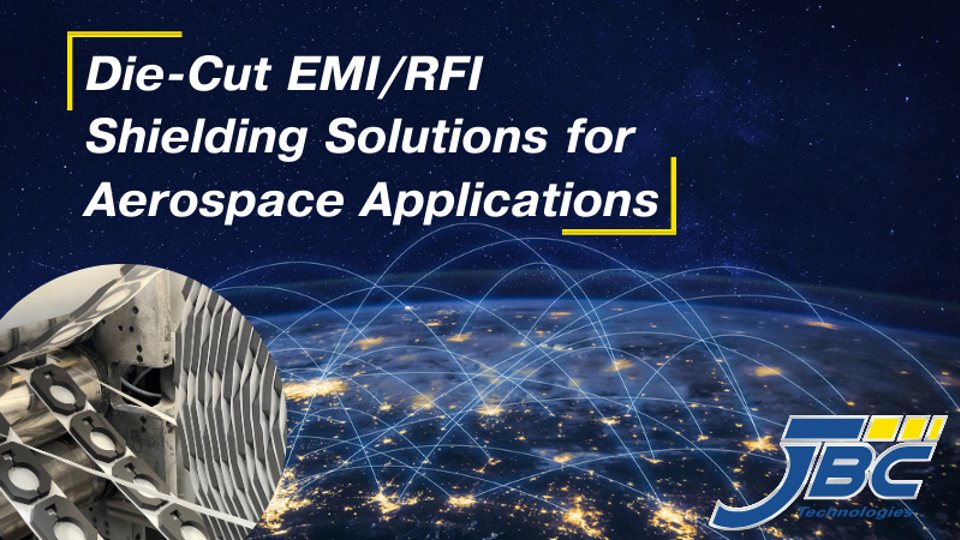
Why Die-Cut Flexible Materials Outperform Metal Shielding Alternatives
Electromagnetic and radio frequency interference (EMI/RFI) is everywhere. Everything from man-made sources of technology like powerlines, industrial machinery, and transmitters to natural phenomena like solar flares, cosmic radiation, and lightning creates disruptive EMI/RFI. If not properly protected against, EMI/RFI can cause major headaches for sensitive electronic aerospace components like communication, navigation, and flight control systems. EMI/RFI shielding performs the important job of protecting these sensitive systems for optimal performance and safety.
Thanks to their strong conductive properties, metals have traditionally been the go-to for EMI/RFI Shielding. The issue? Metal shields are heavy, rigid, and tough to scale across complex designs. For aerospace applications that demand lighter, adaptable solutions that still deliver great shielding, advancements in material science have paved the way for a high-performance alternative: Die-cut flexible materials. Die-cut flexible materials provide EMI/RFI shielding properties with added flexibility, scalability, and reduced weight.
Swapping Weight for Flexibility and Scalability
Often integrated with thin metal coatings or filled with conductive metal particles like silver, aluminum, and copper, die-cut flexible materials offer many key benefits, including:
-
Weight savings: Compared to metals, flexible materials are significantly lighter, helping increase performance as well as fuel efficiency.
-
Conformability: Unlike rigid metals, flexible materials can fit complex geometries without sacrificing performance. This is important for conforming to tight, densely packed electronic compartments.
-
Scalability: The die-cutting process allows you to seamlessly scale your production processes from low-volume prototyping to large volumes of identical parts.
-
Customization: The ability to combine multiple flexible materials to create the perfect high-performance material tailored to your application’s specific needs is invaluable for finding materials that meet the demanding needs of aerospace environments. Custom materials, custom solutions!
Flexible Solutions
Let's take a closer look at a few flexible EMI/RFI shielding alternatives...
Conductive Elastomer Gaskets
Made of flexible synthetic rubber, conductive elastomer gaskets integrate conductive particles to create a lightweight, conformable shielding option. Elastomer gaskets can be cut into a wide range of shapes and sizes, like rings and strips, making them a strong choice for providing EMI/RFI shielding to areas where tight seals are needed to protect against contaminants like dirt and dust. Filled with nickel-graphite particles, BISCO’s EC-2130 is one lightweight, conformable option for EMI/RFI shielding in cramped electronic compartments. With a UL-94 flame resistance rating, EC-2130 provides ancillary flame protection as well. |
![]() |
Low Outgassing Electrically Conductive Silicones
![]() |
With a wide range of conductive fillers available, low outgassing electrically conductive silicones are a versatile option for EMI/RFI shielding in extreme space environments. Made with nickel, graphite, silver, or aluminum, conductive silicones provide effective shielding in many different forms, including gaskets, rings, seals, or sheets. Silicone also boasts flame retardancy and a large thermal range, which is important for withstanding the extreme temperatures of space. Because it's nearly impossible to repair electronics in space, it's critical that your EMI/RFI shielding material meets the proper outgassing requirements to prevent the release of volatile compounds, which can damage electronic systems. Materials like SSP2529, low outgassing electrically conductive silicone, help protect electronics from harmful condensation caused by the release of volatile compounds. |
Conductive Films
Thin films, like polyethylene terephthalate (PETs) and polycarbonates with silver coatings (PCAGs) combine the flexibility of plastics with the shielding capabilities of thin metal coatings like silver, aluminum, and copper. Equipped with a conductive copper grid, 3M Transparent Conductor Film 3M23-MS is one flexible PET option for EMI/RFI shielding, providing excellent electrical conductivity. Conductive films also commonly have ancillary benefits like thermal control and brightness mitigation effects, making them a diverse option for many aerospace challenges. Working with a converting partner to combine PETs and PCAGs with other performance materials is the key to achieving a multi-purpose functional material tailored to your specific needs. Films like PETs and PCAGs are very easily converted and can be laminated to a wide range of other materials, prior to being cut to your finished shape and integrated into your product. |
![]() |
Check out our last blog featuring PETs and PCAGs for their brightness mitigation capabilities!
Conductive Fabric Tapes
![]() |
Providing effective shielding in a thin flexible package, conductive fabric tapes are a durable option for providing EMI/RFI shielding over tight-angles and irregular surfaces. Conductive fabrics like Polymer Science’s P-SHIELD fabric tapes combine the flexibility and conductivity of nickel and copper plated fabrics with acrylic pressure sensitive adhesives for a high-performance adhesive solution perfect for tightly packed electronic compartments |
Conductive Adhesives
Silicone and acrylic adhesives loaded with conductive fillers (nickel, silver) simultaneously shield and adhere for a strong multi-functional bond. 3M’s Electrically Conductive Transfer Tape 9703 is one such example. Filled with silver conductive particles, 3M 9703 remains flexible and conformable while meeting low-outgassing criteria critical in aerospace settings. The thin, flexible nature of adhesives also makes them optimized for scalable automation and assembly initiatives. | ![]() |
Pro-tip: For orbital satellite applications, pair conductive adhesives with microchannel liners to create a safe, durable bond in harsh space environments. Microchannel liners have a series of small tunnels that prevent air pockets from forming under the adhesive by allowing air to be pushed out during application. |
Material Type |
Pros |
Cons |
When to use: |
Conductive Elastomer Gaskets |
-Lightweight -Flexible -Good thermal range (-55 °C to 200 °C) |
-Moderate Shielding: (60-80 dB) -Durability: (Requires reinforcement under extreme conditions) |
Best for areas where small, tight conductive seals are needed. |
Electrically Conductive Silicones |
-Lightweight -Conformable -Low outgassing ability -Good thermal range (-70 °C to 200 °C) |
-Cost -Degrades faster than metal -Moderate Shielding (Maximum level is 100 dB versus the 120 dB of metals) |
Best for areas where outgassing and thermal stability are essential. |
Conductive Films |
-Lightweight -Conformable -Cost-effective |
-Moderate shielding capabilities (40-60 dB for Aluminum, 70-90dB for copper, 80-100 dB for silver) -Durability (laminate to add structural integrity) |
Best used in large areas where moderate EMI/RFI shielding is needed due to ability to mass-produce and scale efficiently. |
Conductive Fabric Tapes |
-Very lightweight -Conforms to very irregular surfaces -Durable
|
-Moderate shielding -Cost -Less adhesive strength compared to silicone |
Best for tightly packed electronic compartments with complex geometries where moderate shielding will suffice. |
Conductive Adhesives |
-Shielding and bonding functionality -Thin, flexible, conformable -Customizability -Automation |
-Shielding limit -Must comply with out-gassing needs of space |
Best for tight spaces with complex geometries, or for bonding materials in EMI/RFI sensitive areas. |
Getting the Most Out of Your Material
While these performance materials are great on their own, without a converting partner, they're just raw potential. Working with a trusted converting partner like JBC Technologies is the key to transforming high-quality materials into high-performance, usable components.
Precision: Tight tolerance die-cutting makes extreme precision possible, allowing flexible materials to fit in very tight spaces with precise measurements, like densely packed aerospace electronics compartments. Ultimate Precision for any application, big or small. |
![]() |
Scalability: Able to quickly go from small-volume prototyping for fit, form, and function testing, all the way to high-volume automated production on rotary die-cutting presses, a custom converting partner scales alongside your production needs. Think thousands of identical parts, quickly. |
![]() |
Customization: Struggling to find the perfect material for your project? Working with a converter opens the door to a world of customization, allowing you to laminate multiple materials together to create the perfect custom solution for your specific needs. Custom materials for custom solutions. |
![]() |
Value-added services: A converting partner strives to add value whenever possible during the manufacturing process. Part presentation considerations like gapping, kiss cutting, and intricate island placement all aid post-processing and automation initiatives. Adding value without subtracting quality. |
![]() |
About JBC Technologies
JBC Technologies is an ISO 9001:2015 Certified flexible materials converter with over 35 years of experience providing custom die-cut EMI/RFI shielding, gasketing and sealing, brightness mitigation, and vibration dampening solutions to the aerospace industry and beyond. Working essentially as an extension of your engineering team, JBC Technologies strives to integrate into your production process, providing full life cycle support from material selection and rapid prototyping to full-scale automation and post-processing needs through value-added engineering and supply chain optimization.
Do you have an aerospace challenge you need help solving? Contact us today to get started on your next project.