Die-Cut Performance Material Spotlight: FLEXcon® OMNI-WAVE™
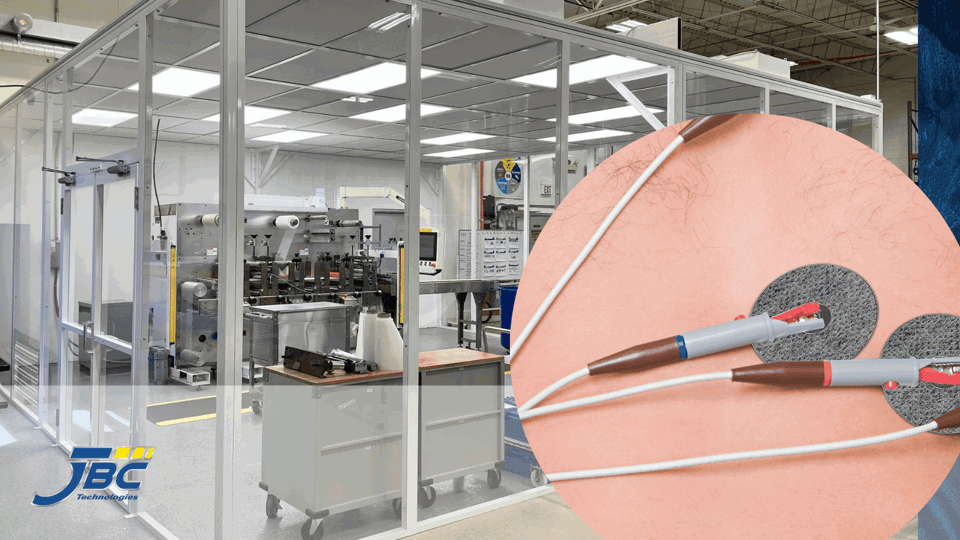
A Hydrogel-Free Bio-Signal Sensing Transfer Tape for The Growing Wearable Device Market
Wearable devices that are worn on the skin to collect real-time data are a rapidly growing segment of the medical device industry. In fact, medical wearables in the global diagnostics and therapeutics marketplace is valued at $26.8B in 2022 expected to grow at a CAGR of 23.5% year over year till 2030. The global disposable EEG electrode market size was valued at USD 695.6 million in 2020 expected to grow at a CAGR of 3.5% from 2021 to 2028.
Whether gathering medical information from CGM systems, EKGs, TENS, or other wearable devices, medical practitioners have long relied on hydrogel-based electrodes and sensors to monitor a patient’s vitals. However, clinical studies show that 8-10% of the population experience adverse skin reactions to hydrogels. This presents a niche market for hydrogel-free technologies.
As a continuation of our series spotlighting the innovative materials offered by our key suppliers, today we are highlighting FLEXcon’s OMNI-WAVE™, a skin-friendly medical grade conductive adhesive that is free of hydrogel or Ag/AgC.
This Q&A features insights from Aditi Subramanian, Strategic Business Unit Manager of Healthcare for FLEXcon®.
Q: What is OMNI-WAVE™?
A: FLEXcon® OMNI-WAVE™ is a signal-receptive media component. More specifically, it is a double-sided, skin-contact, pressure-sensitive adhesive (transfer tape) engineered for short-term wearable and electrode applications. OMNI-WAVE™ has a conductive layer containing carbon fibers that allow medical device sensors or electrodes to send and receive waveform signals. It combines capacitive with conductive biomedical signal sensing to effectively monitor patients without the risk of hydrogel-related skin reactions.
OMNI-WAVE™ is suitable for short-term diagnostic applications such as EKG and sEMG and can distinguish between sympathetic and parasympathetic responses for EDA applications. It is also appropriate for therapeutic applications such as TENS and NMES if a secondary repositionable adhesive is used as a part of the electrode design.
Q: How is OMNI-WAVE™ different than hydrogels?
A: Hydrogels are a “wet” solution that is mostly water and salt. Humidity affects the ability of a hydrogel to conduct signals, limiting a patient’s ability to shower, swim, or even sweat. Air exposure dries out hydrogels, which necessitates expensive foil packaging to protect the product’s integrity. If a hydrogel pack is opened, the shelf life drastically decreases.
As a “dry” double-sided conductive adhesive transfer tape, OMNI-WAVE™’s performance is not affected by humidity. This allows patients to shower, bathe, and exercise normally while wearing the device. So long as it is holding the skin, OMNI-WAVE™ will conduct a steady signal.
Q: What is the construction of OMNI-WAVE™?
A: OMNI-WAVE™ is a double-sided transfer tape with an internal conductive adhesive layer containing carbon. It is topped with a 1.5 mil ultra-smooth polyester release liner that provides ultimate smoothness and flow-out of the adhesive, making it ideal for roll-form converting. It also features a 44 lb. polycoated natural Kraft release liner.
FLEXcon can customize OMNI-WAVE™ constructions to meet a wide array of converting and end-use requirements. This includes options for a release liner, carrier film, adhesive thickness, and other variables.
Q: What is the wear time for OMNI-WAVE™?
A: OMNI-WAVE™ currently offers a 3-day wear time. It also provides a three-year out-of-pack shelf-life, offering cost savings to both manufacturers and end-users when compared to hydrogels. We do plan to iterate this technology platform to continue to create solutions that match what tomorrow’s wearable medical devices will require.
FLEXcon also offers a line of dermaFLEX skin-friendly adhesives that can act as an overtake to help achieve up to 21 days wear time.
Q: What is the back story surrounding OMNI-WAVE™?
A: OMNI-WAVE™ has been under development with FLEXcon’s R&D team for quite some time. Initially, it started as a material solution for batteries. In light of the IP landscape and the patentability of the product, however, it was soon identified as an ideal solution for healthcare wearable applications.
Today, OMNI-WAVE™ is a cost-effective, transformational replacement for hydrogels in many wearable medical device applications.
Q: How did you validate the efficacy of OMNI-WAVE™ in the medical wearables market?
A: FLEXcon® OMNI-WAVE™ bio-signal sensing transfer tape adhesive has been tested for ISO 10993-10 biocompatibility (irritation, sensitization) by an independent testing agency specializing in biocompatibility. The adhesive also meets the requirements of AAMI/ANSI EC-12. Independent clinical studies show that the performance of OMNI-WAVE™ is equivalent to hydrogel-based electrodes.
OMNI-WAVE™ is an approved component in customer 510(k) and CE-marked finished good medical devices and meets internationally accepted standards for quality. It is also:
- FDA-approved components or use in electrodes and wearables
- REACH and RoHS-compliant
In addition, OMNI-WAVE™ won the 2023 Med-Tech Award for Materials Innovation and Worcester Business Journal 2023 Manufacturing Excellence Award for Top Product -Design & Innovation. OMNI-WAVE™ was also a finalist in the 2023 Best of Sensors Awards for Wearables and Medical Technology
Q: What do you think is the most important thing for end customers to look for in a converter? Why is JBC a good fit?
A: Working in the medical device market space requires collaboration with a converter that can achieve high standards. Medical device manufacturers and OEMs need a converter that can align with ISO9001, clean room requirements, and more. A converter like JBC has expert knowledge, industry-leading equipment, and vertically integrated converting capability to produce die-cut parts with even the most exacting standards.
Choose JBC Technologies as Your Die Cutting & Material Converting Partner for Wearable Medical Device Applications
When creating wearable medical devices, it is important to bring a converting partner into discussions early in the design process. Our team at JBC brings expertise to optimize every step of the way, from material selection, to design for manufacturability, to prototypes, and long-term high-volume production solutions. Our sophisticated rotary die-cutting equipment, multiple Class 8 cleanrooms, unmatched process engineering expertise, and strategic supplier relationships further help to ensure you can achieve even the most rigorous specifications. Contact us today to learn how we can help you with your next project.