Die Cut Thermal and Acoustical Insulation
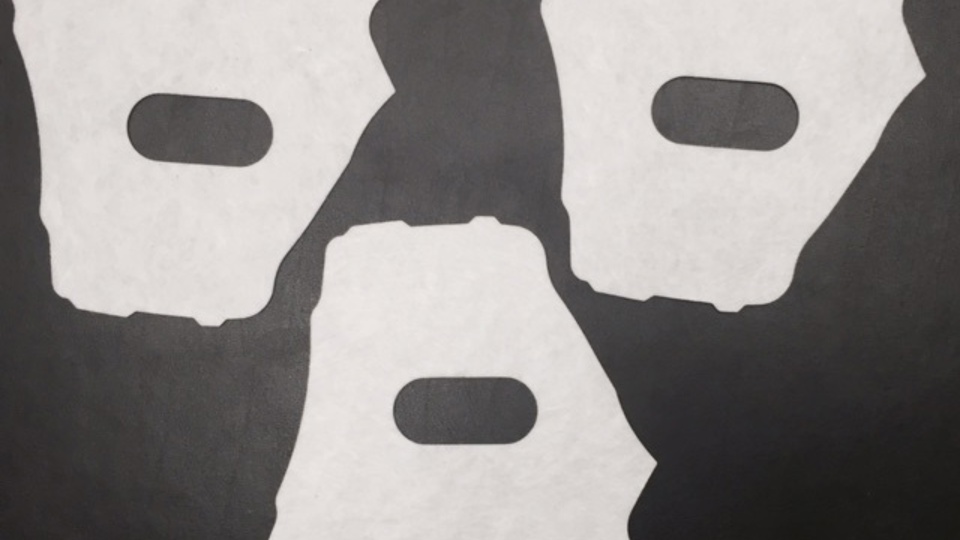
Manufacturers in many different industries incorporate thermal and acoustical insulation into their product designs. Die cut insulation isn’t new, but designers want the latest and most cost-effective solutions whenever there’s excessive heat or noise. To ensure customer comfort and safety, as well as product quality and reliability, engineers look for an edge. Don’t hesitate to engage your die cutter early in the design process, their breadth of expertise in available materials may be invaluable to quickly hone in on a solution.
In their simplest forms, thermal and acoustical insulation are similar. Both limit the passage of energy, whether as heat or sound. For best results, engineers need to choose die cut insulation with properties that address the dominant characteristic of the problematic energy. Material scientists spend years researching the transfer of heat and sound, but you don’t have to be a PhD to apply what they’ve learned. Let’s leave the in-depth studies to these thermal and acoustical specialists, and instead consider what product engineers need to know about thermal and acoustic insulation.
Die Cut Thermal Insulation
Heat transfer is challenging because it occurs in three distinct components: conduction, convection, and radiation.
- Conduction is heat that’s transferred by direct contact. This is what you feel when you touch something hot, like a tray that’s just been removed from an oven.
- Convection is heat that you feel flowing through the air, such as when you put your hand over a furnace duct that’s blowing warm air.
- Radiation is the type of heat that you feel from the warmth of the sun.
Conduction and convection are addressed by using insulation with low thermal conductivity, such as a ceramic blanket or fiberglass. For radiated heat, aluminum foil is a low-cost but effective solution. If you need to address all three components of heat transfer (such as with automotive heat shielding), die cut fiberglass and ceramic blends are a good choice because they offer excellent resistance to conductive and convective heat transfer. Die cut foil can be added to the entire surface, or strategically placed near a “hot spot” such as an exhaust manifold or pipe. In HVAC and furnace applications, a thin piece of die cut fiberglass between two pieces of metal can be used as a thermal break to limit heat flow.
Die Cut Acoustical Insulation
Noise is vibration that is audible. In manufacturing environments, noise is usually caused by machinery. Specifically, vibrations from mechanical movement propagate into components and enclosures. The best way to address noise is at its source. Isolation grommets, damping mounts, and vibration-resistant materials can decouple the source of the noise from metal housings that would otherwise amplify unwanted sounds. If decoupling isn’t possible, use a die cut acoustical material to encapsulate the source.
For example, die cut foam can be used to line metal enclosures and reduce noise levels. Yet all foam isn’t the same. The best acoustical materials for sound abatement are designed to dissipate noise within specific frequency ranges. That’s why it’s important to choose a die cutter that understands the dominant frequency range or ranges behind your noise problem. For best results, pick a partner who also tracks the latest development in noise abatement materials. JBC Technologies provides these capabilities, and can strengthen your product designs with value-added solutions.
Are you searching for solutions to excessive heat or unbearable noise? Are you wondering if there’s a specially-tuned acoustic foam or custom thermal insulation that can meet your acoustical or thermal insulation requirements? JBC Technologies isn’t staffed by PhDs, but our engineers have years of real-world experience with these design challenges. To learn more about our custom die cutting capabilities and material selection expertise, contact JBC Technologies.