How to Leverage Your Die Cutter’s Expertise
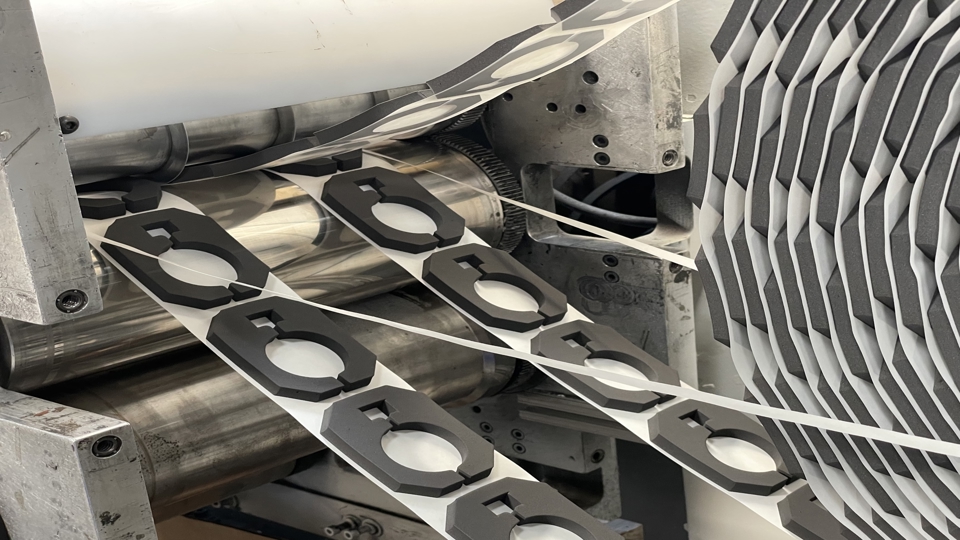
Engineers in the manufacturing industry rely on die cutting experts to help them complete projects on time. Unfortunately, too few engineers know how to truly maximize their investment and get the best value and service from their die cutting resource. If you’re interested in making your current or future association with your die cutting expert worthwhile, keep the following tips in mind.
Discuss Your Project Thoroughly
Let’s face it, anyone who understands die cutting knows it’s a simple process not that much different from baking cookies in the kitchen. Or so it might seem… It’s been our experience that project engineers often see die cutting as this simple cookie cutting process. They dictate what they want based on their die cutting knowledge rather than leaning on the die cutter’s engineering expertise. This can sometimes lead to die cut solutions that may not be optimal. When engaging your die cutter, dream big, think pigs CAN fly and ask for the impossible. You might just be surprised that your die cutter can do things today that weren’t possible a few short years ago.
Choose and Document the Right Material
All too often we see customers turning to old legacy designs to make material selections based largely on what’s worked in the past. Again, we understand that talking to your die cutter in the early stages of a new product design project isn’t going to be at the forefront of your mind, but it should be. Normally we’re engaged at the end of the project, typically when samples are needed and sometimes only after drawings are released. Another interesting phenomena occurs when the engineer, often a recent college graduate, is assigned to create the die cut drawing. They’ll look into their drawing archives and duplicate the material callout used on previous designs. Sometimes these callouts can be a long series of numbers and letters. Other times the callout was incorrect on the previous drawings. In either scenario, errors are easy to make or continue to propagate. This situation can become costly when companies need to comply with ISO standards, forcing drawings to be corrected after release.
Keep Communication Open
Good communication is one of the most important factors of success, which is why it’s important that you and your die cutting expert communicate on a regular basis. Not only should your die cutting engineer be communicative with you, but you should also be accessible to them in case they have questions or a great suggestion after initiating the project. Unexpected problems do happen from time to time. Your die cutter knows that, in most cases, time is of the essence; so keeping an open line of communication in both directions will ensure a successful project outcome.
In addition to helping you tap into your die cutter’s expertise, these tips will ensure that you build and foster a strong partnership. Then, when your next unexpected leak, squeak, buzz, or rattle appears a week before launch, you’ll be able to rest easy knowing that your die cutting partner will have it sorted out in short order.
At JBC Technologies, we offer over 25 years of die cutting experience, ensuring our clients receive the best service and technical know-how in the business. We pride ourselves in having a top-notch team that will guide you through your order, during the production process, and after delivery. Trust JBC to deliver it right every time.{{cta('0e8917ec-a060-4bde-917a-836547262abd')}}