Lamination and Value-Added Die Cutting
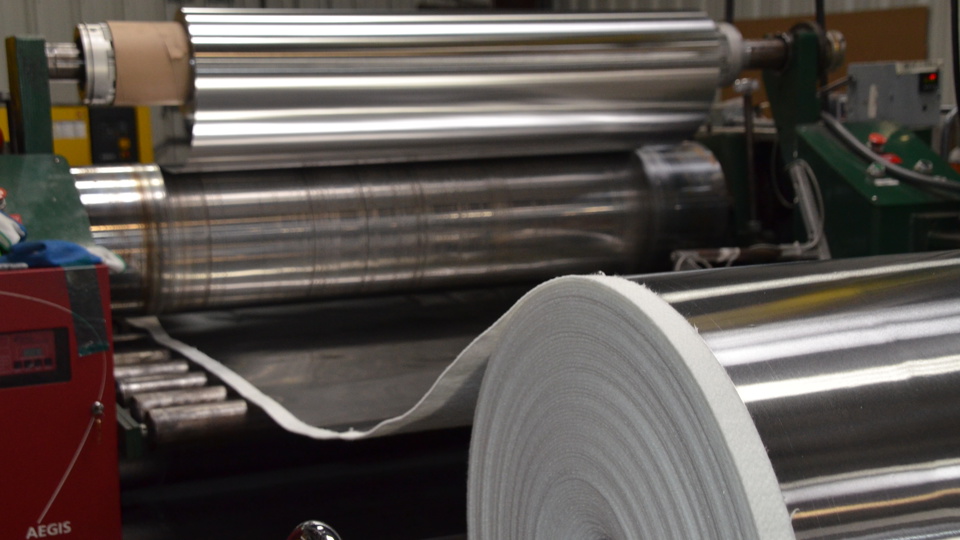
JBC Technologies can create multi-layered laminated materials to impart the physical or performance properties that your application requires. Multi-layered laminations are created when a single substrate cannot provide all the desired characteristics required. Then with our precision die cutting capabilities, whether it’s a one-off prototype or high-volume production, JBC die cuts laminated materials into complex shapes to tight tolerances. By understanding JBC’s laminating capabilities, engineers can leverage our converting expertise for complete value-added solutions.
Multi-Layer Lamination for Die Cut Gaskets
The most common multi-layered lamination is a three-part construction where pressure-sensitive adhesive (PSA) is added to a substrate and the PSA is protected with a liner until it’s removed at the time of use. Whether the substrate is a common paper used for generic labels or a thick fiberglass insulation that needs to be held in place, the lamination processes and performance goals are similar. Materials with unique inherent properties are joined together to achieve an overall objective that’s not possible with an individual material. A substrate like fiberglass has excellent heat-insulating properties and with the addition of PSA, a die cut insulation part can be held in place to ease assembly or remain permanently affixed for the life of product.
Hot Roll and Cold Nip Laminating
JBC Technologies has both hot roll and cold pressure web lamination equipment.
- Hot roll laminating uses heated rollers to soften and activate an adhesive while applying pressure as the substrates are nipped between the rolls.
- Cold laminating requires the introduction of a tacky adhesive whether it be a PSA or sprayed hot melt adhesive. The rollers are not heated and simply apply uniform pressure across the web that causes the materials to bond together by the adhesive.
Depending on the material and your other application requirements, JBC Technologies can use either process to achieve the desired construction. Hot roll laminating is a good choice for many materials that are not heat-sensitive (such as high-temperature insulation). Adhesives used in hot roll lamination processes are solid in form and have no tack or adhesion properties at room temperature. Hot melt adhesives are available in webs like a solid film or a spun bond construction that have a fabric look-and-feel. Spun bond adhesives also provide permeability and breathability which is not available in a pressure- sensitive tape construction.
Sometimes, substrates are needed that are challenging to laminate. These “low surface energy” materials can repel adhesives and make laminating difficult. When these situations are encountered, JBC Technologies can use its corona discharge treatment capability to achieve a suitable bond. This process increases a material’s surface energy using a low-temperature corona plasma discharge.
Add Value to Your Die Cutting Project
Whether your laminated construction requires thin film layers only a few thousandths of an inch thick or a lamination made of many layers that’s several inches thick, it’s not a problem for JBC Technologies. We have the equipment to die cut such a wide range of materials and thicknesses that we can work with you to create the optimal solution specific to your application without compromise. To learn more about our converting and die cutting capabilities, please contact us.