Rotary vs. Flat Bed Die Cutting - Making the Right Choice:
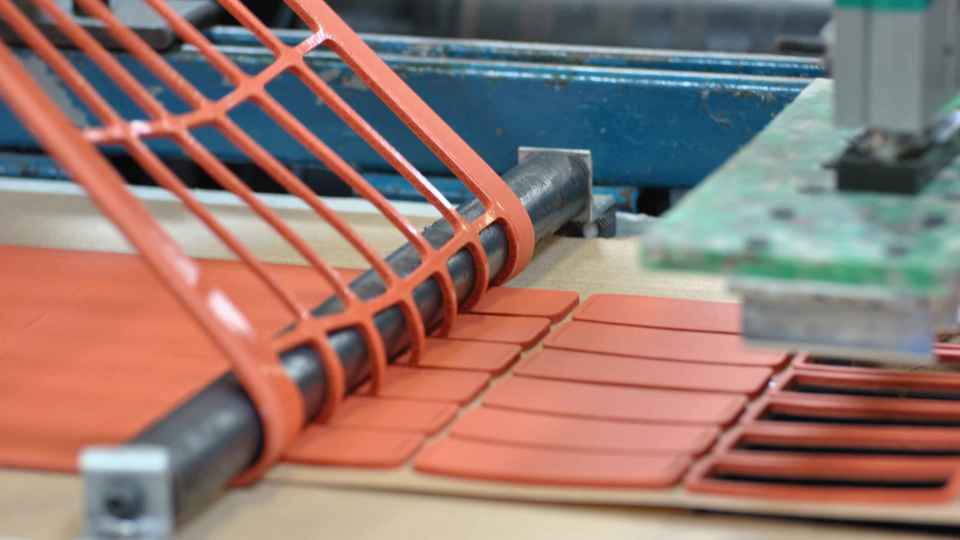
Ten voices are pressuring you to get your product launched. You don’t have time to worry about how someone can produce enough die cuts fast or accurate enough to silence the rattle, stop the leak or hold the assembly that’s become a show stopper one week before your launch date. Good news. You don’t have to. A precision die cutter can handle it.
When it comes to cutting, forming and shaping soft materials, die cutting is one of the best processes for the job. Not only does it ensure high accuracy, but it can also deliver cut shapes quickly.
Two of the most popular types of die cutting are: rotary die cutting and flatbed die cutting. Below is a summary overview of each type.
Rotary Die Cutting
When you think rotary die cutting, think high speed, high tolerance, and high accuracy. Depending on the sophistication of the equipment, rotary die cutting can produce extremely complicated multi-layer parts because of its ability to perform multiple functions in the same processing cycle. Web materials are fed off unwind shafts as the material is pulled into the machine. From the beginning to the end, materials can be laminated, cut, placed and registered in a homogeneous process. Webs go in and finished parts come out. Unlike flatbed die cutting presses there is no lost motion. Material is cut and processed between rotating cylinders. Cutting speeds are measured feet per minute as material travels through the machine.
A great example of a complicated, multi-process rotary die cutting product is the Band-Aid®. A plastic shape is cut and perforated. The cloth middle is also cut then applied, and the peel-back tabs and packaging are all made on the same machine in the same processing cycle.
In addition to stickers and Band-Aids®, rotary die cutting is popular for cutting papers and plastics such as business envelopes, perforated tickets and small cardboard boxes. It is effective for high volume parts produced from thin materials often less than one eighth of an inch.
Flatbed Die Cutting
Flatbed die cutting machines use a flat fixed base and a moveable head. The cutting die is typically made from sharp strips of metal called steel rule, bent in a way that matches the profile of the part to be produced. The bent steel rule is then imbedded into matching slots in a plywood cutting board. The die can be mounted to the base or head. When the machine cycles, hydraulic pressure builds in a cylinder that presses the head with the cutting die through the material. Depending on complexity the base can be a plastic cutting board often used to produce through cut parts or it may be steel as found in precision flatbed die cutting presses.
Precision flatbed presses can through cut or kiss cut similar to rotary cutting presses. Although slower than rotary die cutting, flat bed die cutting machines can open wide enough to process materials too thick to cut with a rotary process. The use of steel rule dies makes Flatbed die cutting an ideal option for short run orders where the expense of a rotary die is prohibitive. Finally, if material is only available in sheets, flatbed die cutting may be the only solution.
Choose a Solutions-Based Vertically Integrated Converting Partner
Whether your cutting solution is rotary or flatbed there are many variants and options available for either method. A good solutions based die cutter will have the ability to configure the most cost effective process for your application. And keep in mind that as technology and automation advances, what was once thought impossible may well be a viable production process today.
Ultimately, you’ll want to work with your precision die cutting expert to decide which cutting method is best suited for your project.