Material Spotlight - 3M 300MP+
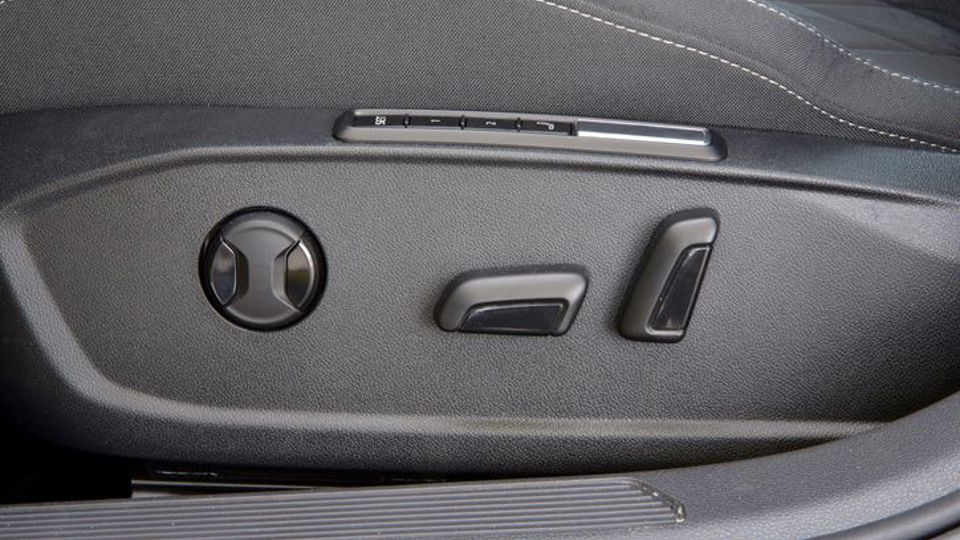
3M 300MP+ - When You Need A High-Tack Double-Sided PSA for Hard-to-Bond Textures
Over the last few years, JBC has highlighted many of the key features and factors to consider when choosing a Pressure Sensitive Adhesive (PSA) for a variety of applications. We know that details matter when it comes to selecting the right PSA. The more you understand substrate surface energies, pressure-sensitive tape constructions, and adhesive tape performance properties, the more likely it is you will choose the best materials for your specific part or product.
Today we are featuring 300MP+ from 3M™, a pressure-sensitive adhesive family that bonds well to porous or roughly textured materials in a low-temperature environment.
What is 300MP+?
300MP+ is a double-sided tape engineered with 3M™ High-tack Acrylic Adhesive that is a drop-in replacement for the legacy 300MP product line.
300MP+ offers a soft, tacky, viscous nature that works especially well on open-cell foams, fabrics, textiles, flocks, felt, leather, wood, and other textured materials. When bonding textured substrates in a low-temperature environment, 300MP+:
- Provides high initial tack and initial bond strength
- Cold flows, grabbing more surface area over time under low temperatures
- Performs as a peel, stick, and press adhesive, avoiding delays produced by clamping, curing, or chemical reactions
This high tack, acrylic PSA lends itself well to automotive interior applications, including seat construction, interior core solutions (fabric attachment, headliners, and bolsters), sealing or gasketing foam attachments, airbag assembly, and attachment, and a peel-and-stick, in-line production fix for NVH and BSR.
300MP+ is also suitable for general industrial, marine, medical equipment, specialty vehicles, construction, appliances, and even sporting goods (inside helmets) and footwear (orthotics and foam insoles). It is even ideal for peel-and-stick DIY products such as decorative tiles and flooring.
Click the graphic above to see the full product brochure.
300MP+: Q&A with a 3M™ Application Engineer
As part of our partner blog series, JBC recently sat down with Nick LaBelle, Advanced Specialist Application Engineer with 3M™ to discuss the development of 300MP+. As we mentioned above, the 300MP+ is a drop-in replacement for a legacy line of 3M products. What we didn’t mention is that this product was fast-tracked after supply chain disruptions escalated the need to get the product to market extraordinarily quickly.
With no further ado, let’s dive into the meat of the interview:
Why was 300MP+ developed?
3M™ developed 300MP+ to replace our legacy 300MP adhesive during the height of the pandemic supply chain crunch about seventeen months ago. Then, in April of 2023, one of our suppliers had a catastrophic facility fire and declared force majeure, eventually closing their plant. We quickly took proactive action to move the product development along to create a more robust supply chain for our customers.
How fast were you able to launch the 300MP+ once the need became apparent?
3M™ began introducing 300MP+ to customers and partners in mid-May of 2023. We were able to share data, technical bulletins, as well as sample materials with customers and end-users. By the first week of June 2023, 300MP+ was in production. 3M™ was already making materials that had completed qualifications and we had an abundance of inventory on hand to help customers transition, test, and perform validation processes. Our goal was to help ensure that customers could seamlessly shift to 300MP+ without any major hiccups in production, efficiency, or cost.
3M™ teams did an incredible job launching this product within a tight timeframe, minimizing end-application disruptions for our customers.
How is 300MP+ different from the original product line?
300MP+ is still a durable, high-tack acrylic adhesive, but the + is there for a reason and that is to indicate that it is a slightly different product. 300MP+ remains viscous and tacky at colder temperatures, enabling it to dissipate more energy and maintain bonds. This makes it ideal for applications with dynamic loads or impacts.
The key differentiating characteristics of 300MP+ include:
- Low fogging under the SAEJ1756 standard, making it ideal for automotive applications.
- Lower Glass Transition Temperature (Tg), making it suitable for low-temperature performance applications. Tg for our legacy product was -32°C while Tg for 300MP+ is -60°C.
- Better capability for static shear strength. Can do more work under a static load.
It’s also worth mentioning that both the legacy and the new adhesives were/are solvent-less and perform well at high temperatures up to a maximum of 250°F.
Can you explain why the 300MP+ line of adhesive tapes is good for “hard to bond” textures?
The soft, tacky, viscous nature of 300MP+ enables it to flow and grab surface area on highly textured surfaces. For example, some automotive parts are injection molded or rough cut with a tool. Molding or cutting leaves a rough texture on the part. A firmer adhesive will only touch the part’s top layer, limiting surface contact and creating insufficient bond strength. This can lead to parts failing or falling off. In contrast, 300MP+ has a thick adhesive coat weight that flows and grabs valleys of a textured substrate, creating more surface area for a bond and achieving mechanical interlock. |
What do you think is the most important thing for end customers to look for in a converter? Why is JBC a good fit?
Most companies today need solutions that help reduce labor costs. Die-cut, converted parts are easier to automate, which helps customers achieve this goal. Working with an expert flexible materials converter like JBC adds exactness and efficiency to automated processes. JBC also brings to the table versatility, cutting-edge equipment, value-add know-how, and prototype services that help OEMs along every step of material selection, design, and production.
JBC Technologies ensures you select the right pressure-sensitive adhesive tape and custom die-cut solution
JBC Technologies is a 3M™ Preferred Converter and 3M™ Medical Materials & Technologies Preferred Converter, Avery Dennison ADvantage Converter, and Berry Global Elite Converter. Our team and the experts at our various manufacturer partners work closely with you and our adhesive tape manufacturer partners to determine the best tapes for your application. With over 35 years of custom die-cutting experience and state-of-the-art manufacturing facilities in four states, we deliver high-quality solutions for customer applications in a variety of industries, including automotive, medical, electronics, HVAC, and appliances. Contact us today to get started on your next custom die-cutting project.