Material Spotlight: Construction Layer Tapes for Medical Wearables
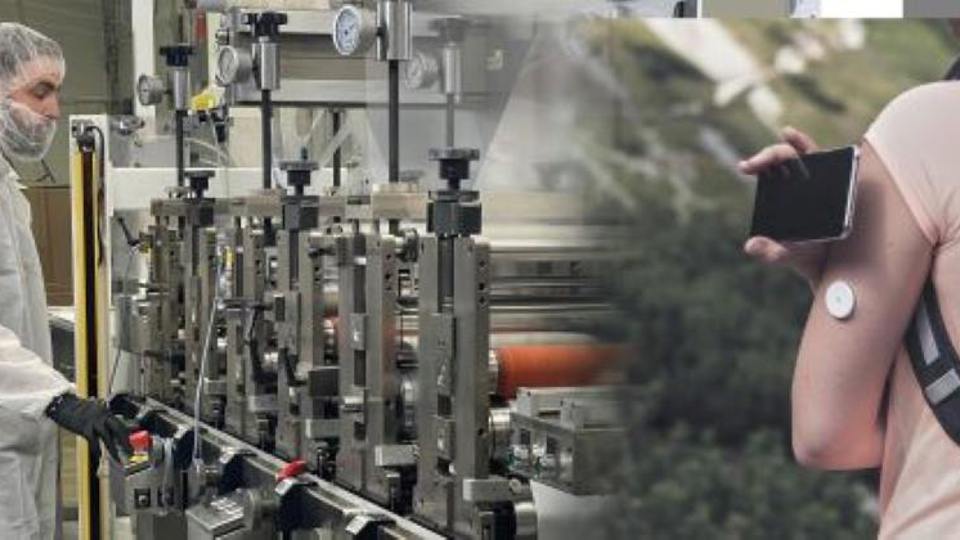
Valued at USD 39.2 billion in 2023, the wearable medical device market is expected to reach 68.9 USD billion by 2030, growing at a CAGR of 11.5% from 2024 until 2030. The prevalence of chronic diseases and the rapid advance of wearable technologies continue to contribute to this rapid growth.
This growth requires that medical device OEMs introduce specialized products of all sizes, shapes, form factors, and materials. Designing lighter, smaller drug delivery systems, diagnostic monitoring machines, or short- and long-term wear devices for chronic applications also requires innovative adhesive solutions.
While not new to the market, differential double-sided tapes are playing an increasing role in fabricating wearable technology devices – as construction layer (tie-layer) tapes that bond one component to the next and as skin contact tapes that affix the device to the skin.
Today’s material spotlight focuses on several such products offered by Avery Dennison Medical and features insights and information provided by Avery Dennison marketing manager and adhesives expert, Miguel Solivan.
Could a differential double-sided tape be a good fit for your wearable device assembly?
Before we dive into product-specific information, here’s a quick primer on differential double-sided tapes. While a typical double-sided pressure-sensitive adhesive (PSA) has the same adhesive on both sides of a carrier, differential double-sided tapes have a different adhesive on either side of a carrier material. This double-sided adhesive design helps achieve a secure bond between two dissimilar materials. Differential double-sided tapes could be a good fit if you need to bond multiple components within a device. Differential tapes are also useful if your device requires a permanent adhesive on one side and a removable adhesive on the other. Read Differential Double-Sided Tape Defined | The Basics for more in-depth information. |
|
Selecting a tie-layer tape: key considerations
Once you’ve determined that a differential tape will work for your application, the next step is to figure out WHICH tape will work for you. Whether you plan on using PSA tape to bond one layer of the device to another or to affix the device to the skin, you’ll need to consider several factors to understand which tape is right for the application.
With the support of key suppliers like Avery Dennison Medical, the converting experts at JBC Technologies are here to help. The more information you can share at the outset, the better we can help you identify the right tape for your application.
Here are a few things we’ll want to discuss
|
![]() |
Check out this blog post for an in-depth look at Selection Criteria for Skin Contact Adhesives.
Avery Dennison “tie-layer” adhesive tapes
With the basics covered, now it is time to get to the specifics. Avery Dennison Medical differential double-sided tapes include acrylic, synthetic rubber, and silicone tie-layer adhesives that “tie” a skin-contact adhesive to a foam material or other device substrate:
Tie Layer Tapes with ACRYLIC / ACRYLIC Adhesives:
|
|
|
Tie-Layer Tapes with RUBBER/RUBBER Adhesives:
|
Tie-Layer Tapes with SILICONE/ACRYLIC Adhesives:
|
JBC Technologies, taking a collaborative approach to optimize your design
As a custom die-cutter, JBC takes a collaborative approach to optimize the design, development, and commercialization of every customer’s product. We leverage the material science expertise of our material partners with JBC’s state-of-the-art value-add services like slitting, laminating, embossing/microperforating, spooling, rapid prototyping, and clean room manufacturing. This enables us to provide every customer with high-quality, custom adhesive solutions to maximize performance, decrease costs, and improve efficiency.
Contact us today to learn how we can help you convert your design concepts into reality.