Micro-Perforating for Sound Absorption in Automotive Heat Shielding
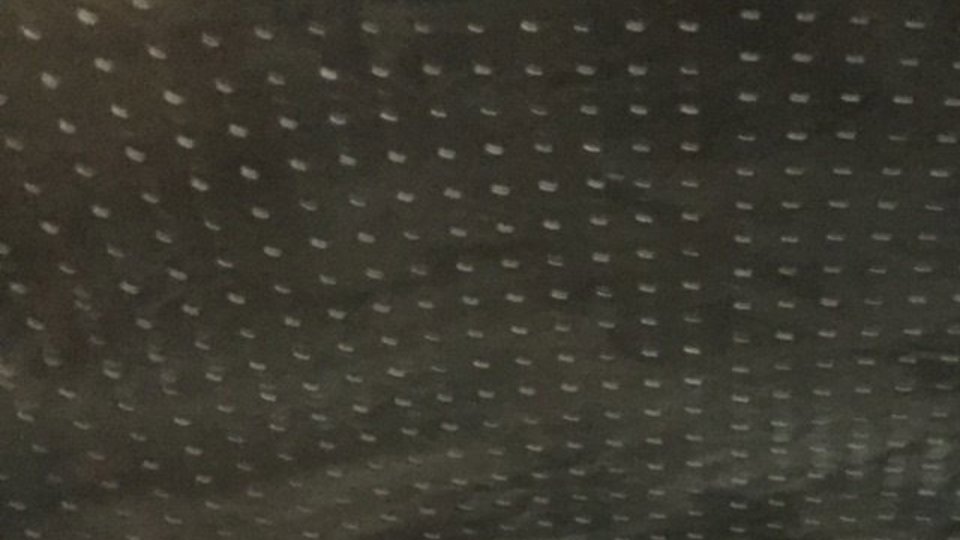
Micro-perforating for automotive heat shielding creates very small holes in aluminum foils. These holes or micro-perforations improve acoustical performance by absorbing noise across a specific frequency range. Heat shield micro-perforating also complements manufacturing processes such as embossing and lamination. For a complete heat management and NVH solution, micro-perforating adds value to automotive die cutting.
Aluminum foils that are micro-perforated also support vehicle lightweighting and can be formed into complex, three-dimensional shapes. Typically, these die cut heat shields are used in engine shields and underbody shield applications. Automotive applications include tunnel shields, inner and outer dash shields, and hood insulators for a cooler, quieter ride.
Heat Shield Designs and Micro-Perforation
Aluminum foils that are micro-perforated can be used in single-layer, double-layer, and sandwich-style heat shields. Single-shell and double-shell heat shields are common, but sandwich-style products provide protection against the highest temperatures. These foil-faced, noise-absorbing structures are thicker, but can still support tight packaging requirements because of their formability.
For NVH designers, it’s important to understand that micro-perforated heat shielding contributes to a net noise reduction. As a rule, thicker foils have a quicker high-frequency roll-off. Thicker heat shields have lower peak-noise absorption frequencies. Heat shield micro-perforation causes a negligible reduction in thermal performance, but hole size remains an important noise absorption parameter.
How Micro-Perforated Heat Shielding is Made
JBC Technologies can die cut aluminum foils in thicknesses ranging from 1 to 12 mil. Many die cutters convert automotive materials, but JBC Technologies provides wide web embossing and micro-perforating of aluminum foils up to 60” wide. We offer a portfolio of aluminum foil products with or without heat-activated adhesive systems for easy adhesion during the molding process. We can also make a custom construction by laminating aluminum foil into multi-layer, sandwich-style material constructions.
Adding aluminum foil to high-temperature insulation enhances the heat shield’s thermal performance as it absorbs high heat and reduce temperatures quickly. When a die cut foil is laminated to the proper thermal insulation, a structure as thin as 1/8” can help to reduce temperatures from 1800° F to 200° F.
Value-Added Die Cutting
Do you need die cut heat shields that are micro-perforated? Are you looking for aluminum foil heat shielding that’s embossed for better formability during the molding process? By partnering with the right die cutter, you can improve your heat shield designs and solve NVH challenges. To find the right solution for your automotive application, contact the JBC Sales Team.