Open Cell & Closed Cell Foams: Keys to Making the Right Selection
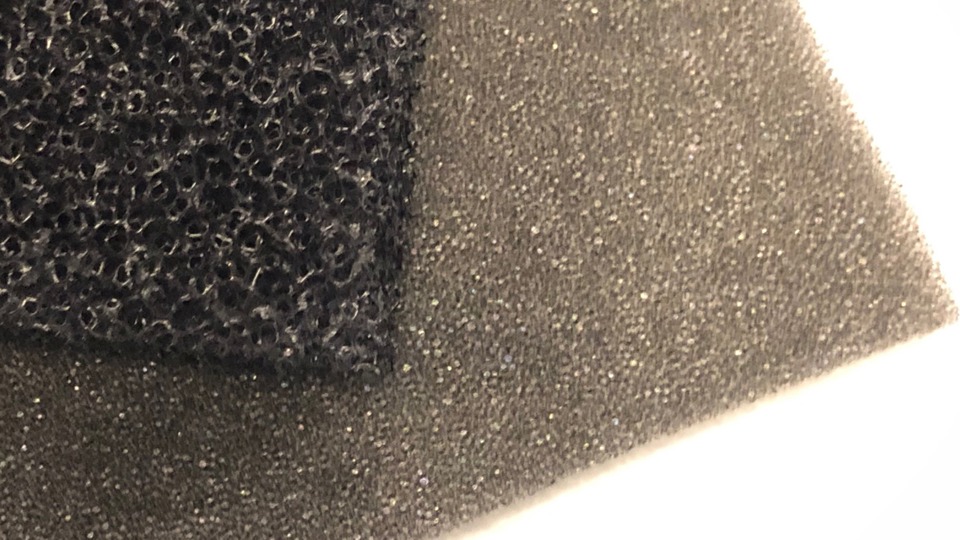
Open cell foam... closed cell foam... What is the difference and why does it matter for your die cut parts?
The differences, we'll address below. As for why it matters, foam rubbers can be used in a myriad of applications and environments, all requiring entirely different performance properties. True, both open and closed cell foams can insulate against heat, vapor, noise and other elements, but to some extent the similarities end there.
Here's a quick primer on the basics. If you are at all in doubt about what material is right for your particular application, we suggest that you consult with the material experts at JBC. We'll work with you to understand your end goal and uncover the material that best suits your needs and budget.
Open Cell Foam
Open cell foam is composed of many of the same ingredients as those in solid rubber. The difference is the addition of a common powder blowing agent, such as sodium bicarbonate. When heated in a mold under low pressure, the rubber material rises (similar to a cake) and the agent reacts with the rubber to create a network of air pockets, or “broken” cells that are not completely walled off from one another. These “open” cells make the foam semi-permeable, offering low resistance to the passage of air, sound, or fluids.
Open cell foam is typically soft, breathable, and springy. It more easily returns to its original shape after compression than closed cell sponges.
Open cell foam is ideal for:
- Sound dampening
- Air filtration
- Cushioning
- Thermal Insulation in dry environments
Closed Cell Foam
Closed cell foam, also known as “expanded rubber or sponge rubber,” differs from open cell foam in that its cells are sealed off from one another, similar to a bunch of grapes. Closed cell foam becomes “closed” when a chemical blowing agent powder or gas-forming ingredient is added to a standard rubber compound. When heat or pressure is applied, the ingredient decomposes and becomes soluble or mixes with the rubber. This process produces a gas that does not degrade the rubber’s cell structure, leaving the closed cells full of air or gas.
As a semi-impermeable sponge, closed cell foam is less affected than open cell foam by issues related to moisture damage (e.g., mold, mildew, rot, bacteria).
Closed cell foams are ideal for applications in which liquid resistance is critical, such as:
- Electrical
- Marine
- HVAC
- Automotive
- Weatherstripping
Closed cell foams are also suitable for insulation, packaging, and more.
Differences Between Closed and Open Cell Foams
Open and closed cell foams differ in many ways, from varying levels of permeability, durability and strength,. Their unique characteristics affect the suitability of each material to various applications and must be carefully considered when making a selection.
Important differences include:
-
Open cell foams must be compressed down to mass or to a semi-solid piece of rubber in order to seal out air, moisture, or other mediums.
-
Closed cell foams achieve an adequate seal upon surface-to-surface contact of the two sealing surfaces with minimal compression or pressure.
-
Open cell foams have a more flexible nature, easily returning to their original state after compression but they have low heat resistance (“R value”). Open cell foam can be manufactured at both high and low densities.
-
Closed cell foams have high rigidity and low density, as well as higher resistance to heat flow.
-
Open cell foams allow air, water and other mediums to pass through, reducing their ability to insulate once moisture is absorbed.
-
Closed cell foams restrict the flow of mediums and are suitable for aiding floatability and maintaining seals and insulation in cold, warm or moist environments.
-
Open cell foams are manufactured in sheets, rolls, molded strips and custom profiles. Open cell sponge sheets typically have a surface impression, as they are molded against a fabric surface.
-
Closed cell foams are manufactured in rectangular sheets, continuous rolls, molded strips or custom profiles by molding, casting, or extruding.
-
Both open and closed cell foams can also be manufactured in buns and then placed through a secondary process (skived, run through a looper, etc.) to achieve final thickness.
Determining whether open or closed cell foam is best for your application takes careful consideration. But that’s just the beginning. Within these two broad categories fall many choices offered by numerous suppliers. Costs, long-term durability needs, moisture, temperature, pressure levels, and more will ultimately inform your selection.
The experts at JBC Technologies are here to help ensure you select the right materials and products for every application, according to each unique specification. Contact us today for more information.