Overcoming Thermal Management Challenges in EV Batteries with eGRAF® SPREADERSHIELD™
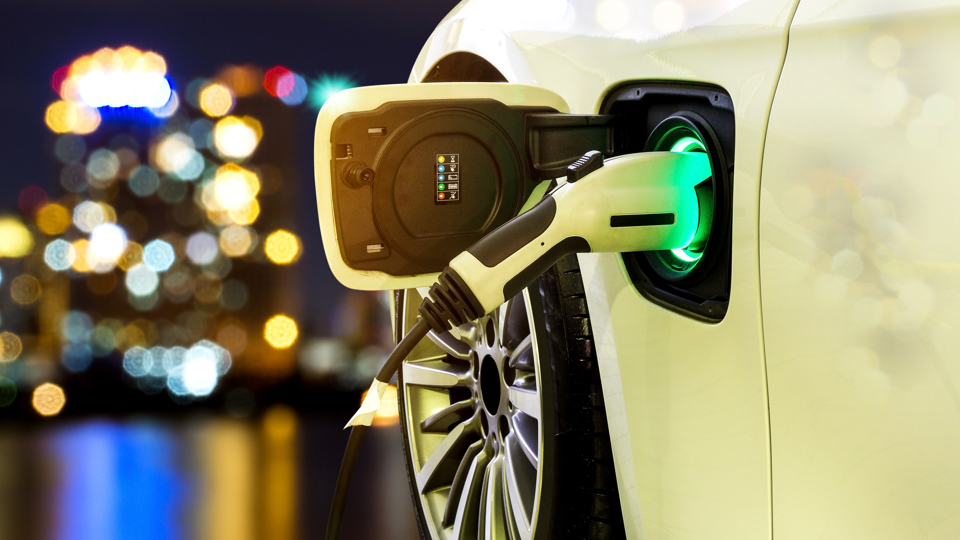
Electric vehicle manufacturers continue to seek out advanced battery technologies and solutions that can address multiple priorities. Balancing the safety and performance of EV battery systems is of particular importance. Designers and engineers strive to achieve improved driving range, faster charging, extended cell lifetimes, and more. Yet, this is no easy task.
In this installment of our material Q & A series, we feature Bret Trimmer, Application Engineering Manager for NeoGraf Solutions, LLC. He discusses Neograf’s eGRAF® SPREADERSHIELD™ flexible graphite heat spreaders, lightweight thermal management materials that are helping EV designers and battery manufacturers improve both the safety and performance of lithium ion batteries.
Q. Tell us about some of the trends you are seeing in the electric vehicle market.
A. Consumer demand for EVs is growing both in the U.S. and abroad. As demand grows, manufacturers continue to seek solutions that help to address an array of priorities. Safety is certainly a big issue – addressing thermal management is a top priority along with performance.
In general, we see manufacturers pursuing four common trends in this market:
- Fast battery charge times
- Extended driving range per battery charge
- Long cell life and battery lifetimes
- Thermal propagation control
Q. What challenges do these trends present to EV designers?
A. Most of the challenges center around thermal management. For example, to achieve a fast cell charge, you must put a lot of energy into a cell in a short amount of time. Putting this energy into a cell can also produce a good deal of heat, which can damage the cell. If a cell gets too hot, that shortens the lifespan and efficiency of a cell, affecting the overall battery lifecycle.
When it comes to achieving extended driving ranges per charge, designers are challenged by how much energy they can put into a battery pack. You can either put a lot of cells into a pack, which helps with driving range, or you can put a good deal of thermal management materials, which helps with safety, fast charging, cell life, and propagation control. You can’t have it both ways. There isn’t enough room in today’s EV batteries for both a lot of cells and thermal management materials.
Designers are constantly balancing these issues – the weight and size of an EV battery and the performance required.
Q. Do designers still typically use aluminum for thermal management in cells and battery packs? Why is that the material of choice?
A. Designers do still tend to use aluminum to address thermal management in EV battery systems. Aluminum is simply what’s known and familiar. It’s a very traditional heat and thermal management material in the automotive industry and is still the most widely used material. But it isn’t the best solution for EV battery systems.
If manufacturers want to achieve fast battery charging, extended driving range per charge, long cell life, and propagation control while using aluminum, the battery is going to be too big and too heavy to be practical.
Replacing aluminum with our product, eGRAF® SPREADERSHIELD™ flexible graphite heat spreaders, enables manufacturers to achieve all of the above in a smaller, safer, and lighter weight battery package.
Q. Tell us more about how eGRAF® is helping EV manufacturers better address thermal management?
A. Most importantly, eGRAF® SPREADERSHIELD™ accomplishes the same heat spreading as aluminum – but at half the thickness and one third of the weight. For a typical EV battery pack, switching from aluminum to our flexible graphite product results in a weight savings of around twenty kilograms (forty-four pounds). In addition, for the same energy capacity and charge/discharge cycles, the size of the battery pack can be reduced by several centimeters in both the length and the width.
Q. How does eGRAF® compare to other materials offered by competitors?
A. In the EV battery space, eGRAF® SpreaderShield is a pretty unique material offering thermal performance while reducing space and weight in one solution. Our product helps to cool battery cells during normal charge and discharge operations and prevent propagation in the event of a cell failure.
In addition to being a better solution for addressing thermal management in EV battery cells, eGRAF is also more flexible. This enables it to maintain good thermal contact with cells as they expand and contract during normal charge and lifetime cycles.
Our product can achieve all of this without adding much weight to the battery system. We are pretty unique.
Q. Can you elaborate on the heat spreading capabilities of flexible graphite?
A. eGRAF® can achieve over twice the heat spreading capability of aluminum. Aluminum can conduct up to 180 W/m·K. Our products can achieve 300-1600 W/m·K.
Q. Outside of EVs, what do you see as the top battery applications for eGRAF®?
A. eGRAF® is ideal for applications anywhere that manufacturers use battery powered propulsion systems, as they don’t want internal combustion engines because of pollution or safety (e.g., docks and ports where you have cranes, trucks, forklifts, etc.)
It is well suited to industrial marine applications, such as ferry boats and diesel-electric hybrid cargo ships, where it is critical to have systems that are safe, reliable, compact and lightweight.
It is also ideal for grid storage battery systems that need compact, reliable solutions. In addition to expected lifetimes of up to 10 years, these systems must also be able to prevent thermal propagation in the event of a cell failure.
Q. Can you share some customer success stories?
A. Customers in the marine industry have been the first to go all in on battery propelled vehicles and eagerly adopted eGRAF® solutions. This industry needs safe, reliable, compact, lightweight battery systems that can meet rigorous propagation standards. They are left to choose between either thick, heavy plates of aluminum between cells or lightweight, low density graphite. eGRAF® SPREADERSHIELD™ flexible graphite heat spreaders are the ideal, economical solution, used as a direct aluminum replacement in these safety-critical battery systems.
Boats and cargo ships in the marine industry monitor each battery cell very closely with battery management systems. They track the functionality of every cell on the ship. With propagation control, if one cell starts to go out of standard, or catches fire they can turn off that module, shutting it off from the rest of the system. It has been a great success.
Q. In your words, can you explain how JBC adds value to your product?
A. Precision die cutting is critical to our product performance and our customers have exacting standards. JBC can cut flexible graphite to any customer specification, accommodating the most intricate die cut requests. We have worked with JBC for a long time and they have been a great partner.
JBC Technologies is an expert at die cutting flexible graphite heat spreading materials. We work directly with NeoGraf Solutions™ to efficiently die cut, package, and deliver quality finished parts and products in a way that reduces costs and simplifies the use and assembly of these parts. We have the technology, equipment, and experts to help you manage any stage of the flexible materials converting process. Contact us today to learn how we can help make doing business easier for you.