Preventing Gasket Failure Part 3: Environment
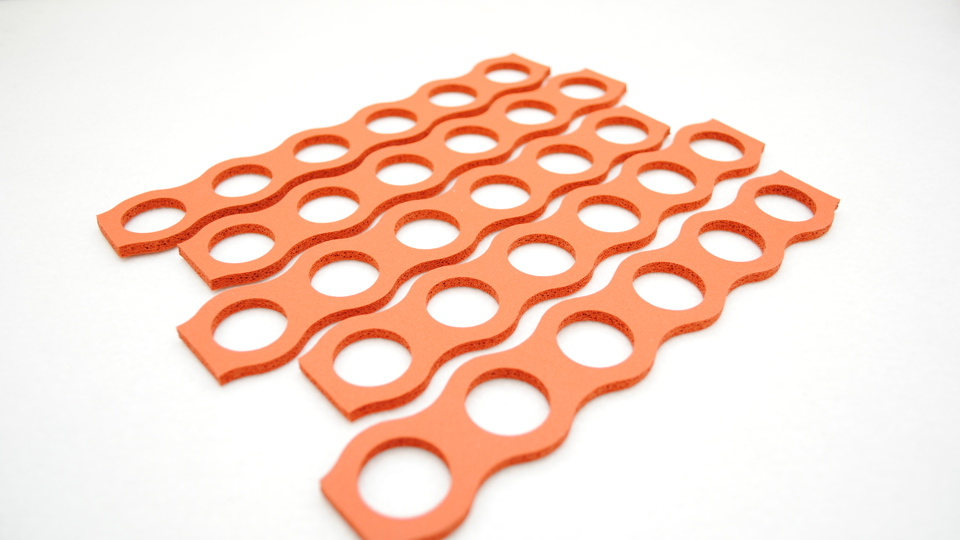
Several environmental factors can impact the longevity of a gasket. Extreme temperatures, moisture, UV and chemical exposure, and even excess vibration can cause a gasket to fail if improper materials are selected. For example, both EPDM and Neoprene are synthetic rubbers that can be made of solid or sponge materials. Both can act as thermal insulators and offer resistance to weather, abrasion and have similar temperature limits. But EPDM provides poor resistance to petroleum products and other chemicals. As a result, Neoprene is recommended over EPDM when similar applications require thermal insulation and resistance to chemicals and oils. As this simple case demonstrates, examining the key characteristics of gasket materials is vital to the success or failure of your product and application.
Today, manufacturers can choose from a wide range of gasket materials that can endure a combination of environmental conditions. We list a few of them here.
5 Common Environmental Requirements for Gaskets
(and examples of gasketing materials well-suited to Meet them)
1. High-Temperature Resistance — Elastomeric Gasket Materials
These gasket materials can endure temperature fluctuations without sacrificing performance.
- Silicone — Available in solid or sponge/foam compositions, silicone demonstrates outstanding properties at both high and low temperatures, as well as strong electrical insulating properties. It also withstands UV, ozone, and oxidation. In addition, it is weather-resistant, flexible, and shrink-proof. Silicone can withstand a temperature range of -67°F to +500°F.
-
Fluoroelastomer — A high-performance fluoroelastomer, Viton™, is well known for its strong temperature, chemical, ozone, and oxygen resistance. It is compressible, lightweight, and provides good thermal insulation. Viton™ can withstand temperatures up to 400°F continuous service.
-
High-Temperature PVC — High temp PVC is ideal for multiple applications and environments, providing a strong, leak-resistant moisture barrier, as well as chemical, flame, and UV resistance. It also offers strong shock absorption properties. High temp PVCs can withstand continuous temperatures as high as 257° F.
2. UV Resistance — Foam
Constant UV exposure can degrade many natural rubbers and nitriles. Open and closed cell foams, silicones, ECH, and EPDM materials can typically stand up to the wear and tear associated with the sun’s demanding rays.
- Ethylene Propylene Diene Monomer (EPDM) Gaskets — Typically a less expensive option to silicone, EPDM gaskets come in both solid and sponge compositions. They are available in a number of densities with varying degrees of hardness and offer strong resistance to UV rays, oxygen, ozone, aging, water, and weather.
- Silicone — Available in solid or sponge/foam compositions, silicone withstands UV, ozone, and oxidation. It demonstrates outstanding properties at both high and low temperatures, as well as strong electrical insulating properties. It is also weather-resistant, flexible, and shrink-proof.
- ECH (Epichlorohydrin) Sponge Rubber — Closed-cell ECH gaskets provide strong resistance to weather, ozone, sunlight, and oxidation. They are also chemical resistant. They are used in many automotive and industrial applications that demonstrate a need for resistance to alcohols, oils, and other solvents.
3. Water Resistance — Rubber
Neoprene (CR), EPDM, SBR, Vinyl Nitrile, PVC, and XLPE closed-cell foams have strong shock absorption properties and are ideal for applications that require a strong, leak-resistant moisture barrier. They also are highly resistant to chemicals, flame, and UV.
- Neoprene is a synthetic rubber that demonstrates strong tear strength and compression set as well as resistance to UV and ozone damage. It is waterproof, corrosion, and flame resistant and, unlike EPDM, provides good resistance to petroleum-based products. Neoprene gaskets can be made of solid or sponge materials.
- Natural Rubber is both water and abrasion-resistant and possesses strong fatigue resistance as well as high tensile and tear strength and good recovery properties. It is often used for anti-vibration gasketing applications.
4. Chemical Resistance — Fluoroelastomer and Neoprene
For the most challenging sealing applications, fluoroelastomers or hardy neoprene may be suitable, depending on chemical exposure. Both of these materials have good compressibility and recovery and can withstand a wide range of temperatures. But they do perform differently when exposed to petroleum-based oils and solvents.
- Fluoroelastomers — For the most challenging sealing applications, a high-performance fluoroelastomer like Viton™ may be appropriate. Fluoroelastomers are known for withstanding ozone, oxygen, hydrocarbon lubricating oils, and typical automotive fuels. They are not ideal for applications exposed to strong acids, alkalies, and ketones.
- EPDM — is a rubber-like material with good compressibility and recovery. It holds up well when exposed to acids and alkalies and is a good choice when dealing with brake fluids or ketones. It does not perform well when exposed to hydrocarbon oils and petroleum products.
- Neoprene — known as an “all-purpose” rubber can tolerate a wide range of temperatures. It is a durable material option that resists flame, weather, abrasion, and petroleum-based oils and solvents such as ammonia, chlorofluorocarbons, and other chemicals.
It should be noted that these materials come with vastly different price tags. so knowing the minimum performance properties you need for your application will be crucial.
5. Reducing BSR and NVH — Open Cell Foam & Microcellular Urethane
Lightweight and flexible, open-cell foams are good for mitigating NVH & BSR, sound-proofing, protective packaging, and applications where air and moisture permeability is needed. Options include Polyether (Ether), Polyester (Ester), Reticulated, and Silicone Open Cell Foams.
Microcellular foams are another resilient material with a low compression set, making them ideal for isolating vibrations. Available compositions include Polyether (Ether), Polyester (Ester), Silicone, Urethane, and high-performance Poron microcellular urethane.
At JBC, our goal is to offer a die-cut gasket solution that provides the best form, fit, and function to achieve its intended end-use. Not only can we help you identify the best foam or sponge rubber material for your gasket or other die-cut application, but we can also help you identify the right pressure-sensitive adhesive and release liner, source the materials, and surface treat, laminate, slit, and construct the composite material in house to any of the foams we cut. Contact us using this easy form or call us at 440-327-4522 and our experts will respond to help you select the best material options for your unique application.