How Pull Tabs Reduce Installation Costs
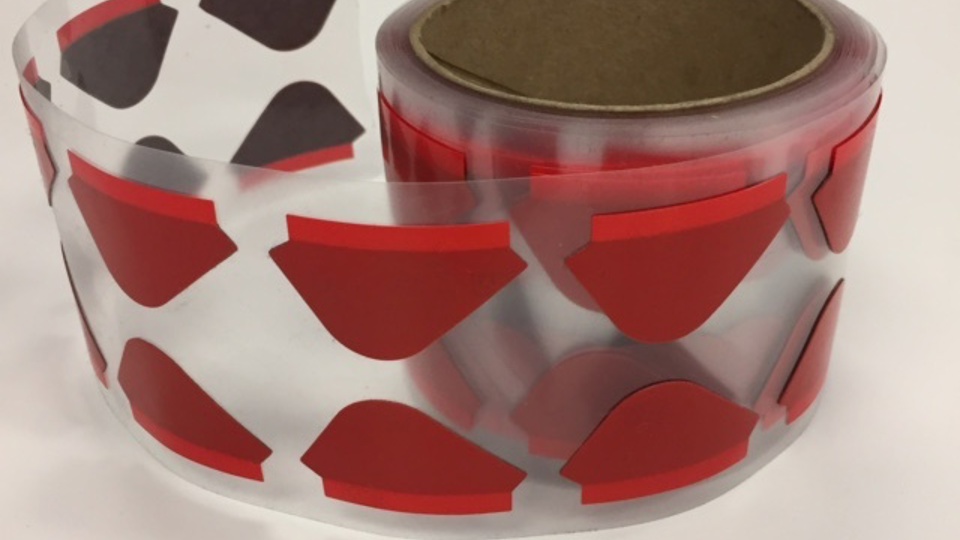
Pull tabs speed the installation of die cut parts. They’re cut from liner materials and provide an edge that’s easy to grab or grasp. Because pull tabs extend from the liner’s surface, they’re also known as extended liners. Pull tabs are produced with rotary die cutting, used with pressure-sensitive adhesives (PSAs), and are sometimes called peel tabs, tear tabs, or tear-off tabs.
Pull tabs reduce installation costs, but the benefits don’t end there. Extended liners protect die cut parts and make smaller parts easier-to-handle. Peel tabs or tear tabs also support the use gloves, a must for workers in many production environments. The time savings that pull tabs provide may seem small at first, but a closer look can reveal a sizable cost savings.
Parts Installation
Across a large number of parts, pull tabs can reduce installation times significantly. Some liners have an edge that’s difficult to find and grasp. For workers, removing these liners can take as many as two seconds per part. By using pull tabs, however, it is possible for workers to save one second per part. Across 1 million parts, that’s a total time savings of 277 hours. Multiplying the total hours by your hourly rate provides your cost savings.
Parts Protection
Pull tabs help to protect die cut materials (such as insulation) that have open structures. When a worker removes die cut insulation from a standard release liner, the insulation can pull apart. That’s because the release value, the force needed to remove the part from the liner’s surface, is stronger than the insulation’s integrity. Pull tabs prevent this pulling apart by providing an edge for workers to grab.
Parts Handling
Pull tabs make smaller parts easier to handle. By providing an extended liner that’s easy to grasp, peel tabs reduce handing times for projects that require fine motor skills. There’s also less waste from part handling errors. Adhesive-free pull tabs even support the use of gloves for hand and finger protection – and without a loss in manual dexterity.
Cut Costs with Pull Tabs
The way that die cut parts are presented for installation is an opportunity for cost savings. That’s especially true in industries (such as automotive) that need high volumes of die cut products. By using parts with pull tabs from JBC Technologies, you can save time and money on your assembly line. You can also get design assistance, help with material selection, and other value-added solutions.
To get started, contact the JBC Team.