Q&A: What you need to know about 3M™ VHB™ GPH acrylic foam tape
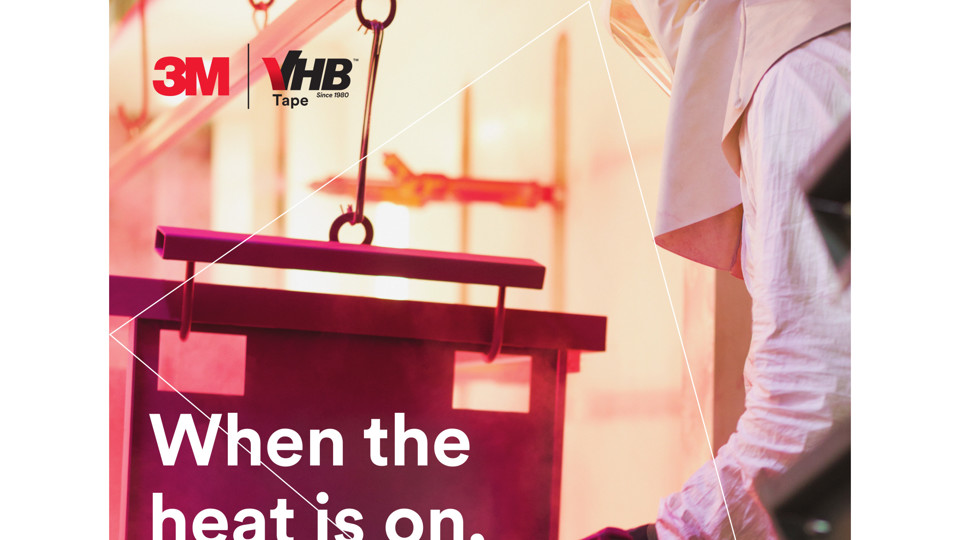
Welcome to the first of our vendor partner Q&A series posts for 2021 – designed to aid you in your gasket material selection by educating you on the features and benefits of the many different materials that we convert at JBC. Today’s post highlights 3M™ general-purpose high-temperature acrylic foam tapes – a.k.a. the VHB™ GPH Tape series. We want to thank 3M applications engineer, Reese Weber for once again agreeing to sit down with us to provide in-depth information on VHB tapes. Links to his past interviews can be found at the bottom of this article.
When and why was the 3M™ VHB™ Tape GPH series of acrylic foam tapes developed?
The VHB GPH series was launched globally back in 2017 and 2018 because our team recognized that while there were a couple of other high-temperature tapes out there, they could not adhere to much other than bare aluminum without the use of a primer. GPH was created to provide greater tack and adhere to more substrates than just metals without needing an adhesive promoter.
Depending on the application, the GPH series may require a primer; however, it was designed to adhere to more substrates without a primer than any other high-temperature tape. For most metals and other medium surface energy plastics it does not require a primer. For a low surface energy application, a primer may be necessary.
What are common applications for die-cut GPH series foam tapes?
Appliance and general industrial manufacturing are two of the most common industries that use die-cut VHB™ GPH acrylic foam tapes. Because they can withstand heat up to 450°F (232°C), they are ideal for use in oven and stove-top assemblies. They also work well as stiffeners and trim pieces in high-heat applications — essentially anywhere high-temperature, high-shear, and high tensile resistance is needed.
In industrial manufacturing, VHB™ GPH tapes’ most common application is attaching stiffeners to panels, which, in most cases, requires roll stock. Die-cut VHB tapes are most often used for attaching trim pieces, logos/nameplates, and other applications where it is important that the tape match the geometry of the part.
Another common use case for die-cut VHB™ GPH tapes in industrial and appliance manufacturing is for bonding components prior to powder coating. This is a unique benefit of GPH due to the high temperatures it can withstand and is important for manufacturers that don’t powder coat in-house. The reason for this is that it eliminates a lot of back and forth and can significantly reduce cycle time. It also improves the aesthetic of the finished part.
What are the top characteristics of the VHB™ GPH series acrylic foam tapes?
- Temperature resistance – Most acrylic foam tapes can perform up to 250°F (121°C). GPH is the “go-to” acrylic foam tape for resisting temps up to 450°F (232°C).
- Fast and easy assembly without the need for skilled labor – This applies to the entire VHB series, but everyone knows how to apply tape. You don’t need skilled labor which is important with today’s manufacturing skills gap. Also, because it bonds so quickly and has immediate handling strength, you can move parts down the line as soon as you attach them.
- Concurrent bonding and sealing – Like other VHB tapes the acrylic foam tapes in the VHB GPH series have a closed-cell core. When they bond they create a seal along the bond line – enabling them to bond and seal at the same time.
- Long-term durability – We consider our VHB tapes to be a permanent bonding tape. It is formulated to last for decades in both interior and exterior applications.
When you say it is a permanent bonding solution, how do you define permanent?
For all practical purposes, it is designed to bond for eternity, but we really can’t test to that level. It is fair to say that it will never need to be replaced if applied correctly. In order to be able to say that with confidence, we run both real and simulated tests. We take the tapes and subject them to extreme weather conditions – heat, cold, extensive UV exposure, and more. Because these tapes are used for critical applications like attaching panels to building exteriors, we’ve run 50-year plus tests and seen minimal degradation of the tapes.
How does 3M™ VHB™ Tape GPH series enable faster product assembly?
The primary reason that this product speeds assembly times is it's quick handling strength. Once you apply it, it is immediately at 30-40 percent of its final bond strength – more than enough to move it down the assembly line for the next step. It will continue building bond strength even after it’s moved down the line, crated, or shipped.
Is die-cut GPH tape an effective gasketing or sealing solution?
Yes, GPH VHB tape is an effective gasketing and sealing solution, particularly when it is die-cut. For a customer who is going to be using the tape as both a fastening/joining mechanism and a gasket or seal, I would almost always suggest die-cutting the tape. If you apply the tape off of a roll there is always going to be a splice point. This could allow for water or air ingress. With die-cutting, you can ensure a precise and seamless cut that does not require a splice.
How does die-cut 3M™ VHB™ Tape GPH series enable lightweighting?
When you think about Lightweighting and VHB you need to think about how the tape really makes an impact. It is not so much that the tape itself weighs less than the screw or rivet, it is more about the options that open up for the substrates you are trying to bond. Once a metal gets too thin, rivets don’t work well and welding can cause heat distortion. Because VHB does not puncture the metal or change its material properties in any way, it enables you to go as thin as you want. This allows design engineers and manufacturers to use thinner gauge materials that cost far less and are more lightweight than traditional alternatives.
What design parameters need to be considered when choosing a VHB™ product?
The two major considerations design engineers need to take into account when specifying a VHB product are adhesion and strength—the substrate the part will be adhered to and the amount of stress it will be subject to. This is applicable for all VHB Tapes. We have a variety of tapes that are really firm that are the strongest VHB tapes, but they don't adhere to much besides aluminum or metal. We also have soft tapes that adhere to just about anything but are not quite as strong as firm tapes. This trade-off between adhesion and strength can help you decide which tape is correct based on the requirements for your assembly.
You also need to consider the environment and temperatures the tape will be exposed to. Not only the constant and intermittent temperatures the finished product will be subject to (such as powder-coating bake cycles), but also the temperature of the environment in which the tape will initially be applied. VHB GPH is designed to withstand extremely high temperatures and our VHB LSE series is the only tape that can be bonded below 32°F (0°C).
How would you differentiate VHB GPH and VHB LSE tapes?
Going back to that strength and adhesion I mentioned above, if you compare the two there is a trade-off. Firm tapes (like the GPH series) have the greatest strength, but they can struggle to adhere to lower surface energy substrates without a primer. Softer tapes (like the LSE series) don’t have as much internal strength but can adhere to more substrates without a primer.
More VHB Resources
VHB Q&A - Joining Dissimilar Materials
VHB LSE Q&A - Joining Materials with Low Surface Energy
Select the right Die-Cut Tape for Your Applications
The experts at JBC offer decades of experience in converting and precision die-cutting flexible materials like acrylic foam tapes for a wide range of industries. Contact us today to learn more about how we can help you with everything from material selection to design, production, testing, and more.