Slug Removal for Die Cutting: How In-Line De-Slugging Adds Value
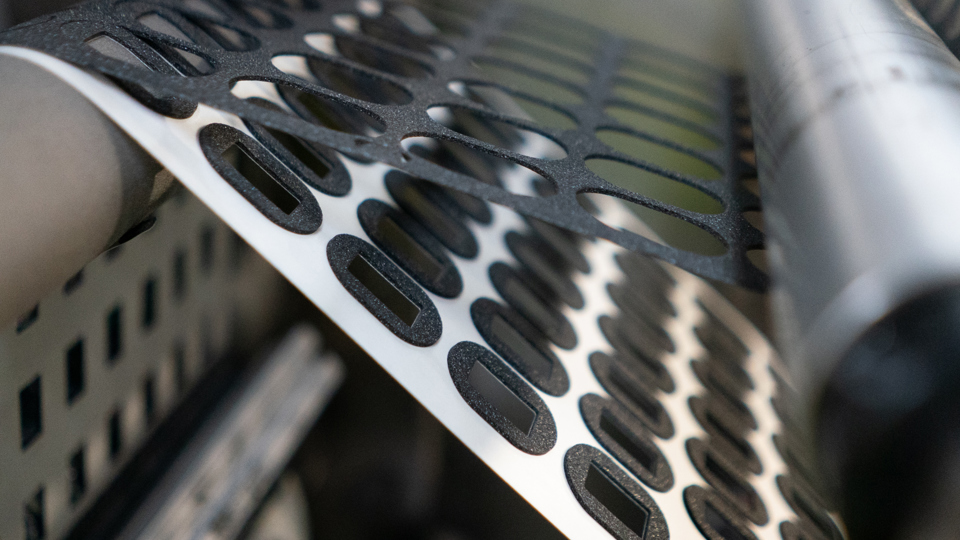
Slug removal or de-slugging during the die-cutting process removes the cut-outs from die-cut shapes. For example, let’s say you need a donut-shaped part. Your die-cutter doesn’t just cut circles from sheet materials or rolls. Instead, your die-cutter uses a tool – the die – to cut a circular part with a hole in the middle. This “hole in the donut" is the slug, the excess material that needs to be removed.
Slugs are more than material waste. Slug removal can add labor costs, extend project timelines, and cause quality control issues. Manual slug removal can be especially problematic. Hand labor is slow, expensive, and subject to human error. If a worker misses a slug, downstream operations may be delayed. Complaints increase, efficiency suffers, and workers must inspect parts and clean-up the discarded slugs.
Fortunately, there’s a better way. Through in-line de-slugging, JBC Technologies can help you save time and money on your assembly line while promoting quality and efficiency.
How In-Line Slug Removal Works
For our customers, in-line de-slugging eliminates manual slug removal and the challenges associated with hand labor. Instead of removing slugs from die-cut products, your employees can perform tasks that add greater value. In-line de-slugging also reduces the amount of time spent inspecting parts, performing rework, and cleaning workstations. Importantly, you can also realize gains from faster operations.
How In-Line De-Slugging Promotes Efficiency
Reducing the amount of time spent handling die-cut parts can provide significant gains in efficiency. For example, let’s say that in-line de-slugging reduces your part handling times by a 1/2 second per part. Across 1 million parts, that’s a total of 138 hours and 52 minutes. To determine how much you’d save in terms of labor costs, multiply the total time (roughly 139 hours) by your labor rate.
Engineers, sourcing managers, and purchasing agents need to understand that parts presentation is a major driver of die cutting costs. By improving the way that die-cut parts are presented for assembly, you can save time and money in production. With in-line de-slugging from JBC Technologies, you can also promote quality. To learn more in-line slug removal for die cut products, contact the JBC Sales Team.