Steel Rule Die Cutting and Product Design
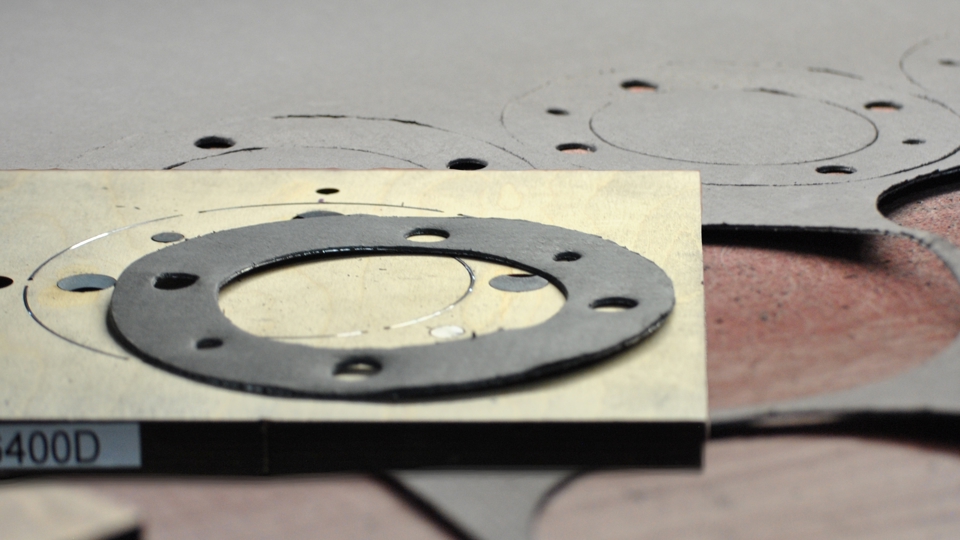
Steel rule die cutting is a cost-effective method for producing die cut parts that do not require extremely tight tolerances. Steel rule dies are much less expensive than solid milled or matched metal dies. The accuracy of steel rule die cutting is a function of multiple factors, including the die’s features, how the die is produced, and the base material to be cut.
For engineers, it’s important to follow some design guidelines to make the most of the steel rule die cutting process. By following these best practices, you can minimize manufacturing risks that can affect part quality. The part design proposed by the engineer can also maximize material yields and cutting speeds while reducing scrap, which helps keep your costs low.
As an experienced steel rule die cutter, JBC Technologies can guide you to a die cut solution that will make you look like a die cutting deity. Let’s examine some of the ways we can help you.
1. Material Selection and Part Layouts
The sheet or web material that’s used in steel rule die cutting is an important consideration. Thinner material is easier to die cut than thick material and, depending on the configuration of the part, adhesive backing can cause slugs to stick in the die. By working with JBC Technologies, you can identify potential issues before it’s time to release your part design to production.
An experienced die cutter like JBC Technologies can also help you to maximize yield based on the part size and the material size. For example, let’s say you want to make a part 7” wide and the selected material is 34” wide. There’s enough material to run four parts across the web, but the steel rule die cutting process would create 6” of scrap.
When you work with the team at JBC Technologies, this dilemma is identified. Investigation into other materials or alternative designs can then begin. It’s not uncommon to encounter situations where the size of a part can easily be reduced by a small amount without affecting form, fit, or function. This small change in part size can reap large rewards by improving material yield.
2. Die Cut Holes and Other Part Features
Often, die cut parts with intricate features and tight tolerances cannot be cut accurately with steel rule dies. To avoid fabrication-related problems such as material cracking, splitting, or tearing, small design changes can make a big difference. For example, if multiple holes are too close together, consider replacing them with a single oblong hole. Another highly beneficial but often overlooked trick is to replace perimeter bolt holes with a curved scalloped cutout. This can achieve the same function, but it eliminates the need to manage and remove slugs.
3. Die Cut Gaskets from JBC Technologies
Do you need steel rule die cutting services that support your part designs? How about die cut gaskets that meet all of your application requirements? Whether your application requires steel rule, matched metal, or a rotary die cutting process JBC Technologies can help you to minimize manufacturing risks, maximize material yield, and ensure a smooth part launch. For more information, please contact us.