Taking the Guesswork Out of Bonding Foams to Curved and Angled Surfaces
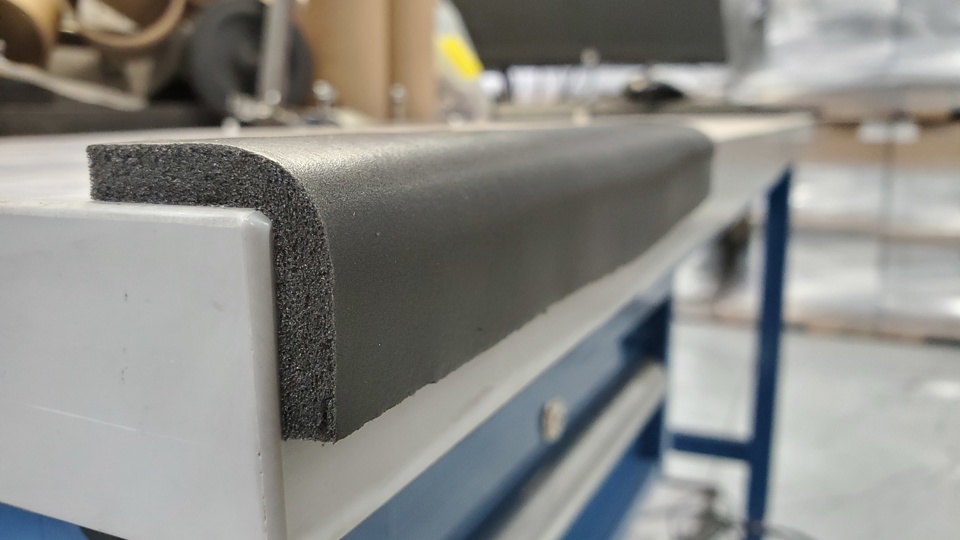
Today's featured blog post comes to us courtesy of our friends at Avery Dennison. Content and images have been adapted from an original presentation titled "Foam Bonding Contours" by Scott Krusinski, Application Engineer at Avery Dennison Performance Tapes.
Successfully bonding foams to flat surfaces can be a challenge all on its own, that’s why it should come as no surprise that bonding those same foams to contoured surfaces or across angles can prove even more difficult. Fortunately, with a little planning and guidance the chances for success can be greatly improved.
In foam bonding applications where the substrate is sharply-angled or curved there are several important things to consider, all of which can play a role in determining whether or not the foam remains securely anchored to the substrate:
- The degree of the contour
- The type of pressure-sensitive adhesive (PSA) tape being used
- The condition of the substrate
- External environmental factors (temperature and humidity)
- The composition of the foam material itself
And if all this isn't enough, oftentimes OEMs don't even account for uneven surfaces or steep angles and bends in their specifications. In many cases choosing instead to conduct their performance testing on flat panels rather than the uneven, curvy surfaces that may represent the real-world conditions experienced by the final application.
Unfortunately, even if we think we’ve taken everything into consideration, there’s still a chance something could go wrong. That’s why knowing what happened and how to fix it can go a long way toward making sure your project goes as planned. Here are three of the most common ways a foam-over-contour installation can go wrong along with some suggestions to help you avoid them in the future.
Adhesive-to-Foam Failure
In this case the failure has occurred because the foam material has pulled away from the foam-side pressure-sensitive adhesive.
Cause | Fix |
Foam is too rigid | Use less dense/rigid foam |
Surface area is too small | Increase overlap length |
Foam side PSA is too firm/has poor bond to foam | Use a different/softer PSA or thicker coat weight |
Angle is too severe | Avoid this design situation |
Adhesive-to-Substrate Failure
In this case, the failure has occurred at the boundary between the substrate and the substrate-side pressure sensitive adhesive.
Cause | Fix |
Foam is too rigid | Use less dense/rigid foam |
Carrier is too rigid | Avoid PET film carriers and try tissue/nonwoven carriers or transfer tapes |
Surface area is too small | Increase overlap length |
Angle is too severe | Avoid this design situation |
Surface energy of substrate is too low for selected substrate-side PSA | Use more aggressive PSA |
Cohesive Split Failure
Now here's an interesting one. The failure in this case is actually within the substrate-side PSA.
Cause | Fix |
PSA is too soft and is splitting due to the stress and possibly high temperature | Use firmer PSA |
Foam is too rigid | Use less dense/rigid foam |
Carrier is too rigid | Avoid PET film carriers and try tissue/nonwoven carriers or transfer tapes |
Surface area is too small | Increase overlap length |
Angle is too severe | Avoid this design situation |
Bonding foams to curvy and angled surfaces can be a tricky endeavor. With so many variables impacting the final outcome, it’s no wonder there are a multitude of ways things can go wrong. Fortunately, with careful planning and some useful tips like those we’ve shared with you in this post, the next time you’re applying adhesive-backed foam to a contoured surface you won’t be the one that gets stuck.