The Anatomy of a Medical Grade Pressure Sensitive Adhesive
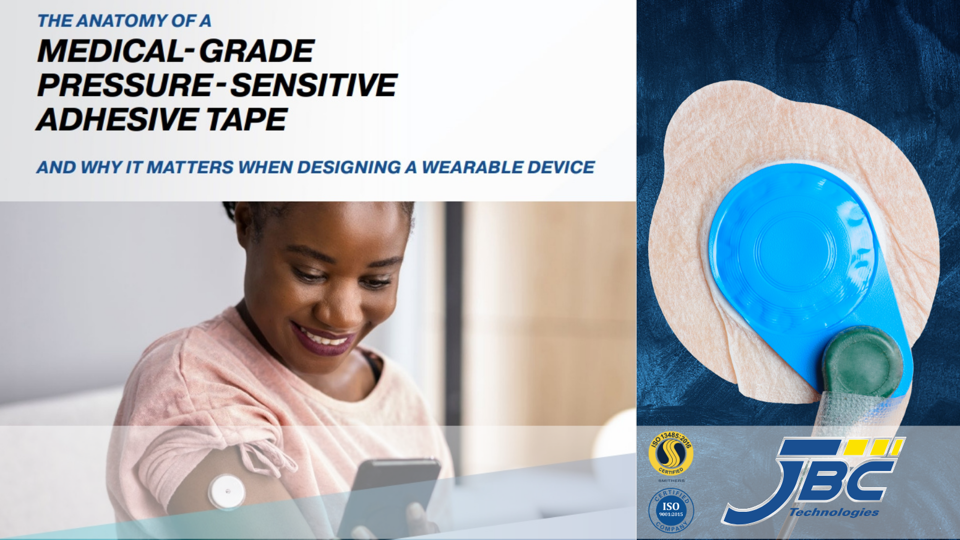
And Why it Matters When Designing a Wearable Device
Unfortunately, not all medical grade pressure-sensitive adhesives (PSAs) are created equally. The high-adhesion, moisture-resistant acrylic-based tape that securely holds a continuous glucose monitor (CGM) patch in place for weeks would be unsuitable for a wound dressing application, where gentle adhesion and repositionability are paramount.
Failing to consider the affordances and constraints of each pressure-sensitive adhesive can spell disaster for your project. Understanding the nuances of what makes each medical adhesive tick (or stick, I should say) is the key to selecting the right adhesive for your wearable medical device project.
How Do I Know Which Medical Grade PSA is Right for Me?
We know that selecting the right adhesive can be difficult, so we’ve put together this comprehensive guide to medical-grade PSA construction to give you the tools you need to navigate even the stickiest situations.
In this white paper, you’ll learn:
-
The key components of a PSA tape (carrier, PSA, liner)
-
The basics of tape construction, including single and double-coated tapes, differential tapes, and transfer tapes.
-
Why having an understanding of tape construction is essential when deciding which adhesive is right for your unique wearable medical application.
Partnering With an Experienced Tape Converter
Selecting the right die-cutting and converting partner is as essential to the success of your project as choosing the correct pressure-sensitive adhesive. Working with an ISO 13485 Certified converter like JBC Technologies eliminates the guesswork from these important design decisions by applying years of material and processing engineering expertise to a wide range of medical manufacturing applications.
Whether it’s nasal strips, boob tapes, wound dressings, CGM patches, or gasketing and sealing solutions, JBC Technologies assists you from rapid prototyping to full-scale production through our diverse converting capabilities optimizing both part and process design along the way.
Contact us today to get started on your next wearable medical device project.