The Role of Pressure Sensitive Adhesives in Automotive Assembly
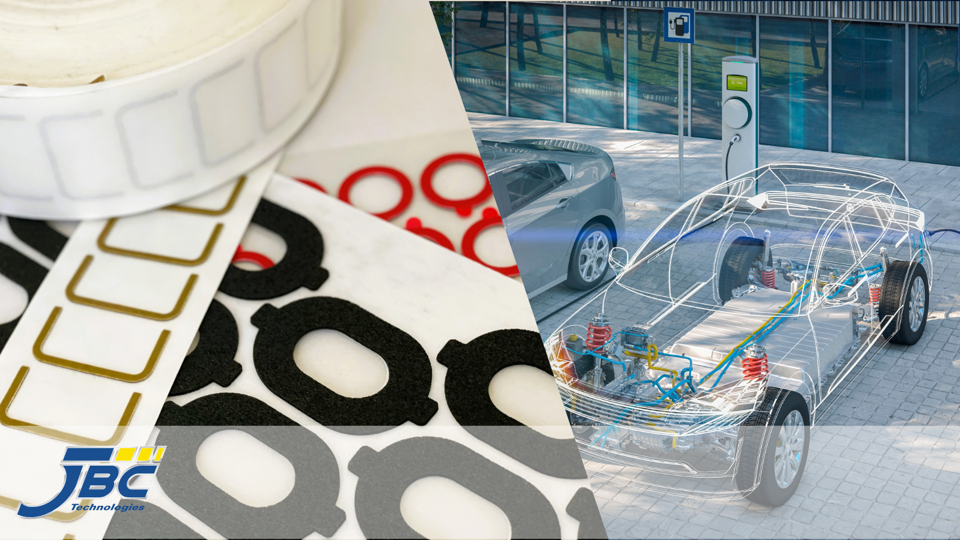
Since the invention of the automobile, car manufacturers have been trending towards more automated manufacturing processes that yield lighter, more efficient products. Thanks to advancements in tight tolerance die-cutting techniques, die-cut pressure sensitive adhesives (PSAs) have become the go-to for automobile manufacturers to ensure quality consistency and provide an optimal product for the consumer.
Before we jump into how die-cut adhesive tapes are integral to automotive production, let's take a step back and review some adhesive basics.
What are Pressure Sensitive Adhesives?
Pressure-sensitive adhesive (PSA) tapes come in many different forms and styles. Understanding what options are available to you is essential for finding the best way to integrate them into your production process.
According to the Pressure Sensitive Tape Council (PSTC), three basic characteristics define a (PSA):
- permanent tack
- adhesion with light pressure
- no liquid-to-solid phase change
Manufacturers design PSAs for use in a wide breadth of applications in automotive assembly. From joining and fastening exterior parts like side-view mirrors, to more complex interior components like display screens and electronic rear-view mirrors, PSAs are literally the glue that holds many components of our modern-day vehicles together. In addition to their structural necessity, they also help deliver a quieter, lighter product to the consumer, playing an important role in buzz, squeak, and rattle prevention for a quieter, smoother ride.
Now, let’s take a closer look at what makes die-cut PSAs such an important part of modern automotive production.
Why are PSAs an important part of modern automotive production?
Production Process Optimization
Material Manufacturers typically supply die-cut PSAs in large rolls or sheets. A specialized converter, like JBC technologies, then takes these large rolls and cuts them into the required shapes using techniques like rotary die cutting and flatbed die cutting, and can even be combined with other performance materials like films or foams to create a multi-functional component, saving time later in the production process. Other techniques like mechanical fasteners or spray coatings also require more manpower and shop footprint to apply.
Enlisting the help of a converting partner can open up a world of possibilities for your project. Utilizing the design experience of a skilled engineering team early in the design process gives you the opportunity to utilize helpful design elements like extended liners and pull tabs. Implementing these options at the beginning stages of development can help automate your production throughput immensely.
Lightweighting
Utilizing the power of PSAs can not only help create a more efficient production process, but it can also yield a more efficient final product. In recent years, car manufacturers have been including more and more plastic parts in their vehicles due to their lower weight and cheaper costs. Because of this, manufacturers have been using PSAs to attach and bond these plastic parts to the vehicle as opposed to the use of welding and rivets. The lightweight nature of tapes combined with the use of lightweight plastics allows auto manufacturers to shed a lot of excess weight, which can yield a fuel-efficient final product. Other alternatives to PSAs, such as mechanical fasteners and dense liquid adhesives, contribute to excess weight, while also being more complicated to apply.
Consistency/Accuracy
Precision die-cutting offers a level of production consistency and accuracy not found in other production techniques. Newer die-cutting technologies such as digital die cutting, waterjet cutting, and multicam CNC routing, grant manufacturers a high level of control over part quality and consistency. Technicians can set up camera systems along the manufacturing line to catch any defects or inconsistencies in real-time, ensuring that each die-cut adhesive meets even the most stringent quality standards.
Consumer Benefits
Die-cut PSAs not only greatly benefit the manufacturer but help deliver a better product to the consumer as well. For example, the low-profile nature of die-cut PSAs coupled with their strong adhesive bond can help create a consumer vehicle with a quieter ride and better air tightness. Die-cut PSAs also help attach interior parts like the touch screen display on the dashboard, or exterior parts like the backup sensor camera. These parts are very important quality-of-life components for a consumer vehicle. These factors, as well as the increased energy efficiency due to lighter weight, all elevate the overall driving experience.
Working with a Trusted Converting Partner
Undertaking a new project can be daunting, especially with the complexity and variety of manufacturing options that are available to you. Enlisting the help of a trusted converter, like JBC Technologies, can help you cut through the noise and find the production path that’s right for you.
From specialty die-cut adhesives to multi-layer laminate materials, JBC provides you with the custom parts to supercharge your project. More than just a material partner, JBC assists in the entire product life cycle from early-stage research and development to full-volume die-cut production. Our status as a 3M Preferred Converter and Avery Dennison AdVantage Parter as well as our talented team of engineering professionals allow us to supply you with the high-performance materials you need and the expertise to tackle any design challenge.
Our vertically integrated production process utilizes a wide array of laminating capabilities that help save you valuable time and production budget.
Contact us today to learn more about what we can do for you and your next automotive project.