Top 5 Reasons You Should Be Using Compound Die-Cutting
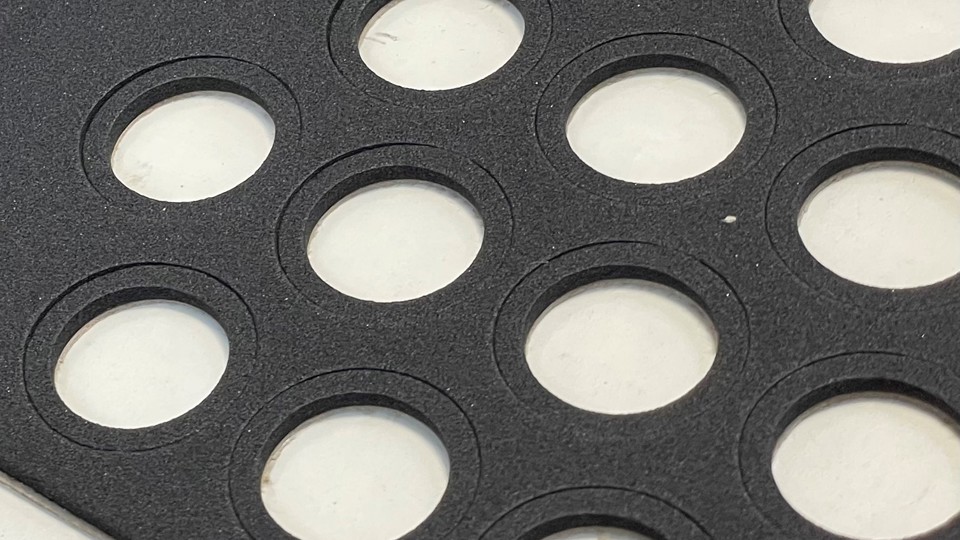
You've developed the product and you're scheduled to launch, but what about the annoying squeak that's suddenly appeared?
As an engineer, the pre-launch squeak is the last thing you want to be dealing with, right? But deal you must, and that's where your friendly neighborhood die-cutting expert can and will come in to save the day.
Die-cutting is different than stamping. Stamping typically involves metal. Die-cutting deals with flexible materials like foam, rubber, and plastic. Whether your squeak needs a rubber gasket or foam liner, a die cutter can help. The best die cutters will offer engineering support to your team before cutting your part, ensuring that what they're making will actually fix the squeak. There are several methods of die-cutting and in this article, we'll be talking about compound die-cutting.
Why Use Compound Die-Cutting?
Die-cutting is more efficient than most cutting methods, especially since it mass-produces shapes with exactly the same dimensions regardless of the type of flexible material used. Unlike stamped die cuts, compound die cutting performs two or more cutting operations in one stroke at one station.
This gasket was made using compound die-cutting. The exterior geometry had to be cut from a large sheet of foam. Then the interior geometry is cut to shape. Rather than using multiple processes to obtain the part shape, compound die cutting utilizes cutting technology that can perform multiple cutting steps in one operation!
1. Compound Die-Cutting Has Fewer Processing Steps
Compound die-cutting creates the desired part shape utilizing a combination of both steel rule and male/female matched metal punches similar to those used in metal stamping. This cutting technology creates intricacy and accuracy in the production of the gasket that bent rule does not offer. Additional benefits include ease in removal of center scrap from the gasket and the ability to create thin walls not possible with a steel rule. This is especially true when cutting hard materials such as fish paper and electrical insulation. Compound cutting technology allows the cutting to run continuously with the help of a feeder if the material is removed in a timely manner, resulting in faster production of the product.
2. Compound Die-Cutting Has Higher Mechanical Accuracy
Compound die-cutting ensures superior accuracy, especially when it comes to the spacing between holes or between the edge of a blank and the edge of a hole. This, in turn, ensures the perfect stock thickness and ultimately prevents distortion. Combine the mechanical accuracy with multi-step cutting, and it's easy to see how compound cutting can save both time and money.
3. Compound Die-Cutting Offers Better Flatness
Flatness, along with good dimensional stability, is an important factor that ensures good runability. It can also affect the presentation of finished paper products such as cards and folders. Compound die-cuts can guarantee good flatness because the materials are pressed by knockouts and punches. As a result, the accuracy of the final product is of high quality.
4. Compound Die-Cutting Smooths the Edges
Any time a material is cut from its original form the possibility exists for the new, or "cut" edge, to be rough. A rough edge can adversely affect the assembly of parts and add material and labor costs to correct it. Compound die-cuts resolve these issues by keeping the rough edges of the flexible material in the same direction. When necessary, rough edge removal will be quicker and easier.
5. Compound Die-Cutting Reduces Scrap
Raw material costs can vary depending on which flexible material is used in the die-cutting process. Because of its high mechanical accuracy, compound die cutting utilizes as much of the raw material as possible, reducing waste, and maximizing cost savings. Improperly set machines and wasted raw material could end up costing thousands of dollars in unnecessary material expense.
So, next time you're faced with an unwanted squeak prior to your product launch, think of using a flexible die-cut material and an experienced die cutter to solve the problem.
Compound Die-Cutting at JBC Technologies
At JBC Technologies we pride ourselves in our ability to offer our customers options. In order to ensure that we can make our customers' custom solutions in the most efficient and economical ways possible, we have to be able to present our customers with a wide variety of performance materials and manufacturing process options. Custom die-cutting is only one of those manufacturing options.
We have over 30 years of custom manufacturing and die-cutting experience and we're ready to put them to work for you today. If you have more questions about custom die-cutting, performance materials or would like to review your project requirements with our engineers, we'd love to hear from you today. Let's fill out our simple new customer contact form and get the process started!