Understanding Pressure Sensitive Adhesive (PSA) Performance Properties
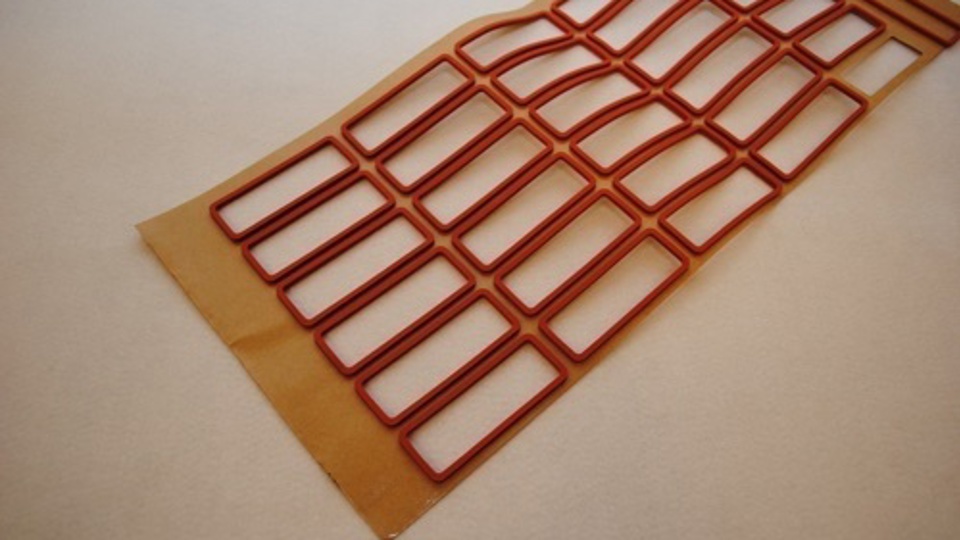
Pressure-sensitive adhesives (PSAs) play an integral part in the functionality of many die-cut gaskets and seals. They are used for everything from permanent fasteners to temporary assembly aids. Applications vary widely and there are multiple types of PSAs to choose from, providing varying levels of adhesion under different types and amounts of stress.
As we mentioned in our last post, choosing the right PSA for your application involves a comprehensive look at your end-use application, the materials and substrates involved, the environment in which the gasket will be used, and the stresses to which it will be subjected. When evaluating stress, the most important performance properties to consider are peel adhesion, tack, and shear.
Peel Adhesion
Peel adhesion is about bond breaking – not bond formation. It is the force per unit width that’s required to break the bond between a PSA tape and the surface to which it’s been applied when the tape is peeled back at a controlled angle (typically 90° or 180°) at a standard rate and condition. Peel adhesion is measured in lb/in. or N/cm and tested according to ASTM 3330M, AFERA 4001, JIS Z 0237-8, or a harmonized international standard.
As a general rule, pressure sensitive adhesives with a high peel value are best suited for applications that require permanent joining. An example would be when double coated tape is used in lieu of mechanical fasteners in automotive manufacturing. On the flip side, pressure sensitive adhesives with lower peel values are better suited for applications that require temporary fastening. A practical application of this would be a release liner on a die-cut part.
Tack
When selecting the appropriate PSA for your die-cut components, the next thing to measure is tack – the initial “stickiness” of the adhesive when it contacts the substrate under very slight pressure. This is important to understand because in some applications you need instant bond strength, whereas in others you need to be able to separate or refit parts.
Tack is measured in units of force (lb. or N) and is determined by the PSA’s ability to “wet” the substrate. Adhesives that “wet” or “wet out” a surface flow across it readily. They maximize the contact area as well as the attractive forces between the adhesive and bonding surfaces.
There are four ways to test for tack: rolling ball, probe tack, texture analyzer, and loop tack. PSAs with low tack generally won’t leave residues behind. This makes them ideal for delicate or decorative surfaces, and for providing temporary protection to finished surfaces. PSA tapes with higher tack setup quickly but don’t support parts repositioning.
Shear
The third property to consider is shear – the holding power of the adhesive based on the PSA’s internal strength or cohesiveness. Like peel adhesion, shear is a function of contact time, application pressure, and temperature. As shear strength increases, however, tack and adhesion performance typically decrease.
There are two types of shear: static and dynamic.
- Static shear is measured by hanging a weight from bonded substrates and measuring the amount of time it takes until the weight drops.
- Dynamic shear is determined by pounds per square inch (PSI) of force required to break that bond and is measured by pulling a lapped joint in opposite directions until it releases or breaks.
PSA tapes with high shear are less likely to split under stress but are also likely to thoroughly “wet” a surface.
It is important to note that adhesive strength is strongly dependent upon the substrate material, so the PSA strength that meets peel, tack, and sheer requirements for one application, may be completely inappropriate for another. That is why it is so important to work closely with your converter during the materials selection phase.
JBC Technologies Can Help
Assistance with adhesive selection is just one of the many value-added solutions that JBC offers to help our customers improve quality, reduce costs, and increase efficiency. Our engineers and technicians have over a century of combined expertise in material selection and product design knowledge. Contact us today to learn how we can help you with your next project.
Related Reading
HOW TO CHOOSE THE RIGHT PSA FOR YOUR DIE-CUT COMPONENTS
DO YOU REALLY NEED A SILICONE PRESSURE-SENSITIVE ADHESIVE?
PART 1: THE BASICS OF PRESSURE SENSITIVE ADHESIVE (PSA) FAILURE
PART 2: THE BASICS OF PRESSURE SENSITIVE ADHESIVE (PSA) FAILURE