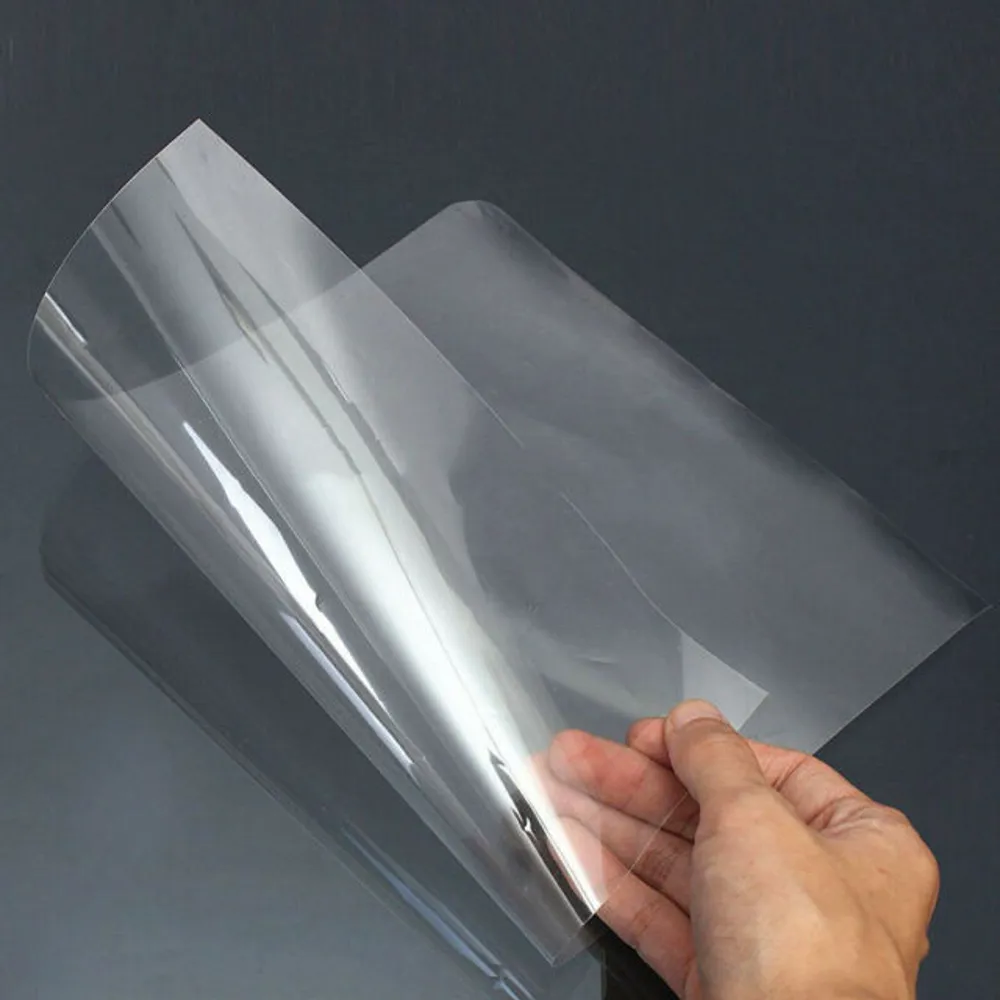
Performance Materials Plastics & Films Custom Die Cutting
For over 30 years, JBC Technologies has used custom precision die cutting and converting for dozens of thin, flexible plastics and polymer films. We can make everything from simple to intricate, large-format to small-batch prototypes.
Polymer films & Plastic Sheets make great gaskets, seals, shims, gap fillers, washers, discs, and insulators.
Our state-of-the-art die cutting processes enable us to cut plastic parts with incredibly tight tolerances, with precision repeatability.
Here's some more information about each of the plastics and polymer materials we have converted over the years to help you choose a material that may be suitable for your next custom die-cutting project.
Thin Plastics & Films for Custom Die-Cut Parts
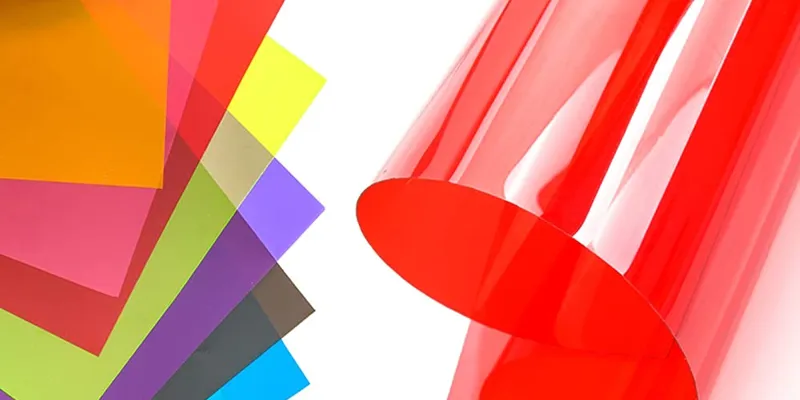
Material & Manufacturing Expertise
- Our engineering and die cutting experts can assist with plastic or polymer film material selection.
- Our network of material suppliers can help with the technical and application details.
Plastics Material Converting
- Lamination of pressure-sensitive adhesive backing
- Slitting or sheeting to size
- Surface treatment
Plastics Die Cutting Capabilities
- High-speed, tight tolerance rotary
- Wide web for cutting parts up to 52” long and 72” wide
- Dieless/Laser/Waterjet for rapid prototyping
Industries Served
Automotive • Medical • Consumer Electronics • Appliances • Aerospace
General Purpose Plastics
Nylon Nylon 66, Nylon 6, Nylon 510
Why Nylon?
- Exceptionally strong
- Relatively resistant to abrasion and moisture absorption
- Excellent chemical resistance
- Washable
Nylon is often used as a substitute for low-strength metals. It is the plastic of choice for components in the vehicle engine compartment because of its strength, temperature resilience, and chemical compatibility.
Typical Uses/Applications
Gaskets • Washers • Curcuit Boards • Spacers • Shims • Wear Plates • Strip/Sleeve Bearings • Retainer Rings
Polycarbonate Lexan®, Makrolon® FD
Polycarbonate is 250 times stronger than glass and is virtually indestructible. Because of its impact resistance, polycarbonate is a favorable choice for protection from extreme weather, flying debris, or vandalism.
Polyester (PET) Mylar®, BOPET
Why PET?
- Crystal-clear thermoplastic
- Excellent water and moisture barrier properties
- High mechanical strength
- Relatively high melting point
Biaxially oriented PET film, or BOPET (often known by the trade name Mylar®), by evaporating a thin film of metal onto its surface, can be aluminized to reduce its permeability and to make it reflective/opaque (MPET).
Typical Uses/Applications
Magnetic Tape Carrier • Adhesive Tape Liner • Beverage/Food Packaging • Automotive Carpet • Glass Replacement
Low-Density Polyethylene LDPE
Why Low-Density Polyethylene (LDPE)?
- Soft, flexible, and lightweight
- Excellent low-temperature flexibility, toughness, and corrosion resistance
- Easy to weld and heat seal
- Good chemical resistance
LDPE is known to have good chemical and impact resistance and it's relatively easy to fabricate and form. While not known for its use in high-temperature applications, LDPE is often used for orthotics and prosthetics.
Typical Uses/Applications
Lunch Boxes • Pharmaceutical Packaging • Trash Bags • Water Pipes & Hoses • Cable Jacketing • Corrosion • Protection
High-Density Polyethylene HDPE
Why High-density Polyethylene (HDPE)?
- Outstanding tensile strength and large strength-to-density ratio
- High-impact resistance and melting point
- Good chemical resistance and vapor barrier performance
- Easily recycled
Thanks to its high malleability, rigid strength, and corrosion resistance, HDPE is the perfect combination of strength, cost-efficiency, and environmental friendliness. HDPE is subject to stress cracking, is difficult to bond to, is flammable, and has poor temperature capability.
Typical Uses/Applications
Wood Plastic Composites • Snowboards • 3D Printing • Food & Beverage Containers • Skeletal & Facial Reconstruction • Cutting Boards • Piping
Acetal POM, Delrin®, Celcon®
Why Acetal (Polyoxymethylene)?
- Excellent resistance to wear and abrasion
- Low moisture absorption
- High tensile strength and rigidity
- Chemically resistant to fuels and organic solvents
- FDA-approved and 100% recyclable
Acetal is a versatile engineering thermoplastic with a fantastic balance of strength, performance, and workability. Acetal can be blended with specialty materials like graphite, rubber, glass, and nanocomposites giving it unique material properties.
Typical Uses/Applications
Small Gears • Valves • Fasteners • Medical Devices • Zippers • Furniture Components • Automotive Door Locks • Plumping • Conveyors
Polyethylene Terephthalate-glycol PETG
Why PET-G?
- High strength and impact resistance
- Food-safe and 100% recyclable
- Excellent chemical resistance against acids and bases
- Good clarity and printability
The G stands for glycol, which, compared to traditional PET, adds durability and strength, and contributes to impact and temperature resistance. PETG's combination of extrusion-friendliness and relative heat-stability (less prone to smoking and unpleasant odor) it's also used to make 3D printing filament.
Typical Uses/Applications
Food & Medical Packaging • Electronic Insulators • Advertising Displays • 3D Printing • EMI/RFI Shielding • Gaskets • Vibration Damping
PTFE Teflon®, Fluon®, Hostaflon®
Why PTFE?
- The lowest coefficient of friction of any solid
- Is completely chemically resistant and inert
- Very tolerant of high temperatures
- Provides excellent electrical insulation and dielectric strength
PTFE has an operating temperature range of -400°F to 500°F and is the most chemically resistant commercial plastic available, unaffected by most corrosive liquids, vapors, and gases. Conforms to both FDA and AMS specifications, making it ideal for medical use and food production.
Typical Uses/Applications
Seals (including PTFE o-rings) • Gaskets • Valves • Wire Insulation • Insulated Transformers • Bearings • Surface Coatings • Pump Diaphragms
Specialty Plastics
FEP
FEP film is a transparent, thermoplastic film or sheet that can be heat sealed, thermoformed, laminated, welded, or metalized to be used in a wide variety of applications. With its ideal balance of chemical compatibility, electrical reliability, wide thermal range, mechanical toughness, and long term weather ability there are numerous uses where FEP becomes an ideal solution. Teflon® FEP is available in thicknesses ranging from .0005” to .020” as well as in specialized cementable versions in the same thickness range.
PFA
PFA film can offer continuous service temperatures up to 260°C (500°F). In addition, Teflon® PFA provides superior creep resistance at high temperatures, excellent low-temperature toughness, and exceptional flame resistance. With these superior attributes as well as enhanced flex life Teflon® PFA can be a upgrade where Teflon® FEP will not service the most demanding design hurdles.
PVDF (Kynar®)
PVDF is a polyvinylidene fluoride polymer. Kynar® & Solef® are noted trade names for this material. It is strong and tough as reflected by its tensile properties and impact strength. It is resistant to creep under mechanical loading. It is stable when exposed to UV and sun light. PVDF has high abrasion resistance, thermal stability and high dielectric properties. PVDF is especially well-suited for applications requiring high purity and superior resistance to acids, bases and solvents. PVDF can be used as insulation for electrical wiring because of its flexibility, light weight, low thermal conductivity and excellent corrosion and heat resistance.
PEEK
Crystalline PEEK film offers an outstanding range of physical, thermal, chemical & radiological properties. PEEK's characteristics include high temperature performance, excellent wear properties, superior chemical resistance, hydrolytic stability and outstanding toughness and strength. PEEK meets many aerospace, automotive, fire, smoke and toxicity, food/water, medical/pharmaceutical, and military approvals and standards. PEEK can be used continuously to 480°F (250°C) and in hot water or steam without permanent loss in physical properties. For hostile environments, PEEK is a high strength alternative to fluoropolymers. V-0 flammability rating and exhibits very low smoke and toxic gas emission when exposed to flame.
ABS
ABS has a strong resistance to corrosive chemicals and/or physical impacts. It is very easy to machine and has a low melting temperature making it particularly simple to use in injection molding manufacturing processes or 3D printing on an FDM machine. ABS is also relatively inexpensive (prices, currently around $1.50 per pound, typically fall somewhere between those of Polypropylene ("PP") and Polycarbonate (“PC”). ABS plastic is not typically used in high heat situations due to its low melting point. All of these characteristics lead to ABS being used in a large number of applications across a wide range of industries.
Porous & Fluted Plastics
Coroplast - Fluted Polypropylene Sheet
Coroplast is a high-quality polypropylene twin wall profile sheet formulated for use in the screen printing, display, and packaging markets. Coroplast uses a copolymer resin in order to increase impact and low temperature performance. Coroplast retains the ability to be flexed an unlimited number of times without breaking. It is chemically inert, with a NIL pH factor and most oils, solvents and water have no effect. Performs well under adverse weather conditions or when exposed to harsh chemicals. Coroplast performs well under adverse weather conditions or when exposed to harsh chemicals.
Expanded PVC Sheet
Rigid expanded foam polyvinyl chloride (PVC) is a material whose extraordinary combination of features makes it ideal for commercial signage. Expanded PVC Sheet is economical, thermoformable, dimensionally stable, lightweight and weatherproof. Brands: Komatex®, Celtec®, Sintra®, and Intefoam®.
Here are just a few of the many material partners we work with:
We also work with customer supplied material. If you have material that you need converted, please reach out to your sales representative or contact us for additional information.
JBC Technologies: Precision Die Cutter, Material Converter Plastics & Thin Films
The sheer number of plastic materials available today can be intimidating and overwhelming. That’s why it’s helpful to work with a die cutting partner like JBC. With our extensive material sourcing network, 30+ years of experience, and diverse technical know-how, we can help guide you toward the best solution for your custom die-cut plastic parts application.
Let us help you choose the plastic or thin polymer film that's a perfect fit for your application.