Performance Materials for Brightness Mitigation in Satellites
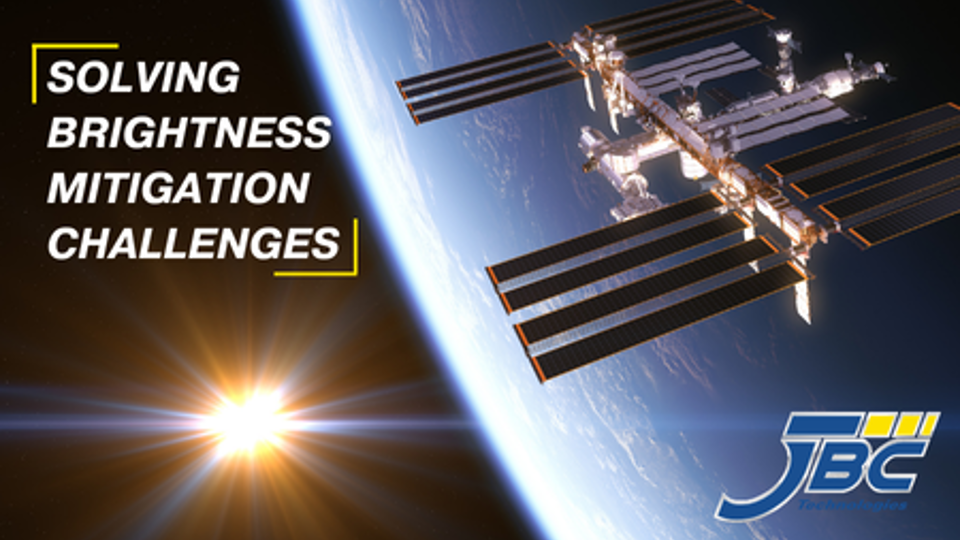
Custom Die-Cut Solutions to Brightness Mitigation Challenges
On October 7th, 1957, the Soviet Union launched Sputnik 1, the world’s first orbital satellite, thrusting the world into a new age of scientific development and space exploration. Since then, about 20,650 satellites have been sent into space, with about 13,660 of these satellites still in orbit today.
While these modern engineering marvels have revolutionized the way we communicate, consume media, and collect data, they have also created a new issue for astronomers: light pollution.
Orbital satellites reflect sunlight down to Earth, obscuring visibility for astronomers attempting to study the night sky. Thankfully, aerospace manufacturers are finding creative ways to minimize their reflective footprint with the use of custom die-cut high-performance brightness mitigation materials.
Solving Brightness Mitigation Challenges
Brightness mitigation is a term that refers to the practice of using highly reflective films to deflect solar rays away from Earth, rendering the satellite invisible to observers below.
But not all reflective films are up to the task, so for design engineers it’s an important balancing act between selecting a material with the right reflectivity that’s also able to withstand the brutal conditions of space. And it is not just about the film. It’s also about the pressure-sensitive adhesive that is used to secure the film to the satellite panels.
We've put together this list of a few high-performance brightness mitigation materials for your consideration. However, the only way to tell if a material is truly right for your project is through working with a converter to complete fit, form, and function, testing to select and approve the perfect material for your project.
Adhesive Tapes for Space Tech Applications
Silicone-Based Microchannel AdhesivesSilicone-based microchannel adhesives are a durable tool for bonding brightness mitigation films to a wide range of surfaces. Combining the durability and temperature resistance of a silicone-based adhesive with a microchannel liner makes a powerful adhesive solution.
Look to silicone microchannel adhesives for: |
|
-
Temperature Resistance: Silicone can withstand extreme temperature changes ranging from -50 °C to 200 °C, helping minimize shrinking risks due to its low coefficient of expansion. When combining multiple performance materials together, like in a multi-layer insulation (MLI) blanket, ensure each material has a similar coefficient of expansion to prevent damaging shrinkage effects when exposed to the extreme temperatures of space.
-
Air bubble prevention: (microchannel liner): The microchannels in the liner act as tunnels for trapped air to be pushed out during application, eliminating any dangerous air pockets from forming. An alternate way engineers address this challenge is by adding perforations that enable trapped air to vent from under the surface. Unlike microchannel liners, however, perforations limit the amount of reflective material exposed.
-
Great adhesion: Because they are able to bond to a wide range of low surface energy (LSE) materials, silicone adhesives are optimal for combining difficult-to-bond materials.
-
Durability: Silicone adhesives are tough enough to withstand the harsh elements of space.
Important considerations:
- Cost: Silicone adhesives are typically less cost-effective than acrylic or rubber options.
- Limited options: Silicone adhesives don't come in as many varieties as acrylic and rubber alternatives.
- Needs silicone liner: Silicone adhesives must be paired with a compatible silicone liner.
When to use:
- Bonding lightweight films like FEPs and PETs to satellites in harsh environments
- Vibration-heavy scenarios
- When low outgassing is needed
- Where air-bubble prevention is critical
Pro tip: Working with a capable converting partner is the key to getting the most out of your silicone adhesives. A skilled converter like JBC Technologies can not only laminate the adhesive to the substrate(s) of your choice and cut to the requisite shape, but they can also offer time saving features like pull-tabs, kiss-cut your adhesive components to a roll for optimized post-processing and handling, or even provide automated assembly solutions, if the volume is high enough to merit. |
Lightweight Reflective Films
Aluminized PET/Metalized FilmsAluminized PET (polyethylene terepthate) films with a thin layer of aluminum area a lightweight, cost-effective option for brightness mitigation where increased thermal control is needed. Look to aluminized PET films for:
|
|
Important considerations:
- High reflectivity: The low solar absorption rate of PETs is a double-edged sword. The increased reflectivity of PET films means that more sunlight gets reflected to Earth, making it a less potent brightness mitigator compared to the mitigation materials mentioned later in this blog.
- Low conductivity: Aluminum is not as conductive as silver, which is another high-performance coating alternative used on brightness mitigation materials.
- Fragile: Aluminum films may tear or puncture easily.
- Moderate thermal ceiling: Limited to about 150 °C.
When to use:
- Best for lightweight, affordable reflectivity where keeping satellite internals cool is essential.
- When cost and weight requirements outweigh brightness mitigation needs.
- Cost-effective option for coverage over large areas where moderate brightness mitigation is acceptable.
- Short to medium length missions.
Pro tip: Looking to fine-tune the brightness mitigation capabilities of your PET without sacrificing thermal control? A converting partner like JBC Technologies can laminate PET films to a Silver Inconel Coated FEP film, combining the brightness mitigating effects of Silver coated FEP with the thermal control of PET. |
FEP with Silver InconelFEP (fluorinated ethylene propylene) films can be coated with silver through vapor deposition and topped with an Inconel layer, functioning as great thermal radiators and brightness mitigators. Look to FEP with Silver Inconel for:
|
|
Important considerations:
- Cost: FEP with Silver Inconel is typically less affordable compared to PET.
- Rigidity: Not as flexible as other materials and may require further reinforcement to prevent cracking.
- Weight: The denser metal layers contribute to increased weight.
When to use:
- High heat rejection needs
- Corrosive sensitive areas
- Long duration, harsh orbits
- High-performance brightness control
Pro-tip: Reserve for high-performance areas; pair with PETs for less demanding areas. It’s important to work with a converting partner who can help provide material selection assistance to ensure you’re using the optimal materials for the job. |
Polycarbonate Films with Silver CoatingsPolycarbonate films with silver coatings combine reflectivity and durability to create a tougher option for brightness mitigation. Look to polycarbonate films with silver coatings for:
|
|
- Cost: More expensive than FEP.
- Lower thermal ceiling: Relies heavily on silver for heat emission.
- Weight: Denser than both PET and FEP.
- Oxidization: Requires an oxidation barrier for long-term use.
When to use:
- Impact-prone areas
- Moderate thermal zones (under 130 °C)
- Prototyping or niche designs
Pro-tip: Through digital die-cutting capabilities, a converting partner like JBC Technologies can provide rapid prototyping support to perform fit, form, and function testing while avoiding any tooling costs. |
Consulting with a Converting Partner
With all the factors to consider when selecting the right brightness mitigation material, it can get overwhelming. Enlisting the help of a trusted converting partner like JBC Technologies is an important way to cut through the noise of the material selection process.
JBC Technologies custom die-cutter and flexible materials converter with over 35 years of experience providing engineered solutions to the aerospace and defense, medical, industrial, battery storage industries, and beyond. From custom brightness mitigation materials to die-cut EMI/RFI shielding, JBC Technologies provides full life cycle support from rapid prototyping through digital cutting capabilities all the way to scaled production. Years of materials and process engineering experience coupled with long-standing relationships with industry-leading suppliers allow JBC to provide innovative, cost-effective solutions. |
Got a project that you think JBC can help with? Contact us today to get started.